Catalysts for green ammonia production and ammonia cracking
Transporting hydrogen through chemical conversion to ammonia is gaining considerable attention as it is expected to be the most cost-competitive solution at the very large scale required. In this method, hydrogen is first converted to ammonia (NH3) for storage and transportation, and then at the point of use, ammonia is reconverted to hydrogen via cracking. As one of the leading catalyst providers in the ammonia-related new hydrogen economy, Clariant offers highly innovative catalysts for ammonia synthesis and its cracking.
Catalysts for green ammonia production and ammonia cracking
Transporting hydrogen through chemical conversion to ammonia is gaining considerable attention as it is expected to be the most cost-competitive solution at the very large scale required. In this method, hydrogen is first converted to ammonia (NH3) for storage and transportation, and then at the point of use, ammonia is reconverted to hydrogen via cracking. As one of the leading catalyst providers in the ammonia-related new hydrogen economy, Clariant offers highly innovative catalysts for ammonia synthesis and its cracking.
Process of ammonia cracking
The ammonia cracking process to reconvert ammonia to hydrogen can take place in centralized large-scale plants located near ports or in smaller decentralized facilities e.g., in urban areas. Centralized and decentralized ammonia cracking each have certain advantages, depending on the intended point of use.
Small-scale ammonia cracking
Decentralized facilities are suitable for small-scale processing of several hundred kilos of ammonia per hour using ruthenium catalysts, for example, HyProGen 850 DCARB, resulting in high-purity hydrogen, e.g., for fuel cell applications. Ideal locations are near filling stations supplying hydrogen for vehicles.
Large-scale ammonia cracking
For large-scale processing of more than, e.g., 1,000 t/d of ammonia to feed hydrogen into the energy grid, major industrial plants are clearly favorable. These can be built to employ proven nickel catalysts like HyProGen 820, 821 and 830 DCARB to meet the needs of industrial consumers like municipalities or steel, cement, and chemical companies.
In most cases, these large plants will have two types of reactors to maximize the efficiency of the plant.
Ammonia cracking process scheme and reactor types

Ammonia cracking process scheme and reactor types
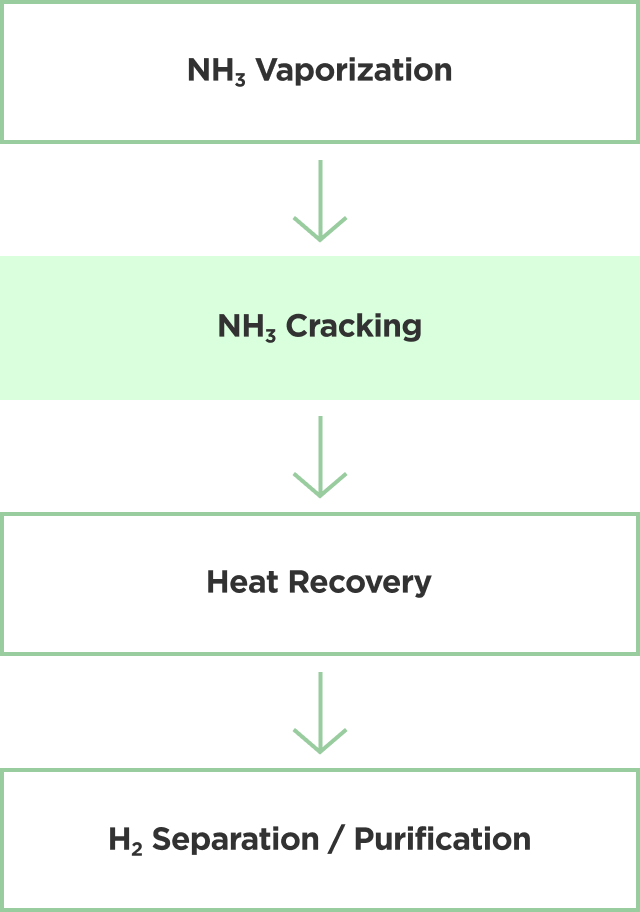
Adiabatic reactors
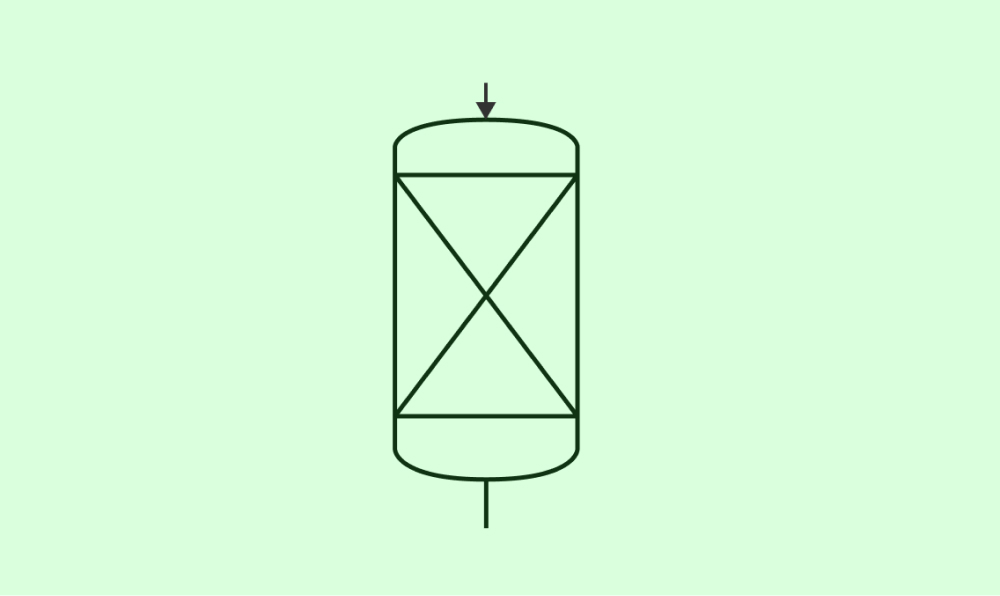
- Catalysts need high activity and can be smaller in size, and demands on mechanical stability are lower
- Full-particle catalysts with high active metal content
- Pressure 20–40 bar / up to 650 °C
Clariant catalysts for adiabatic reactors
HyProGen 820 DCARB: Novel recipe enhances thermal stability, enabling a higher inlet temperature of the adiabatic reactor
HyProGen 821 DCARB: Highly active Ni-based catalyst for low-T application, optimized for bottom layer of adiabatic reactor
Fired tubular reactors
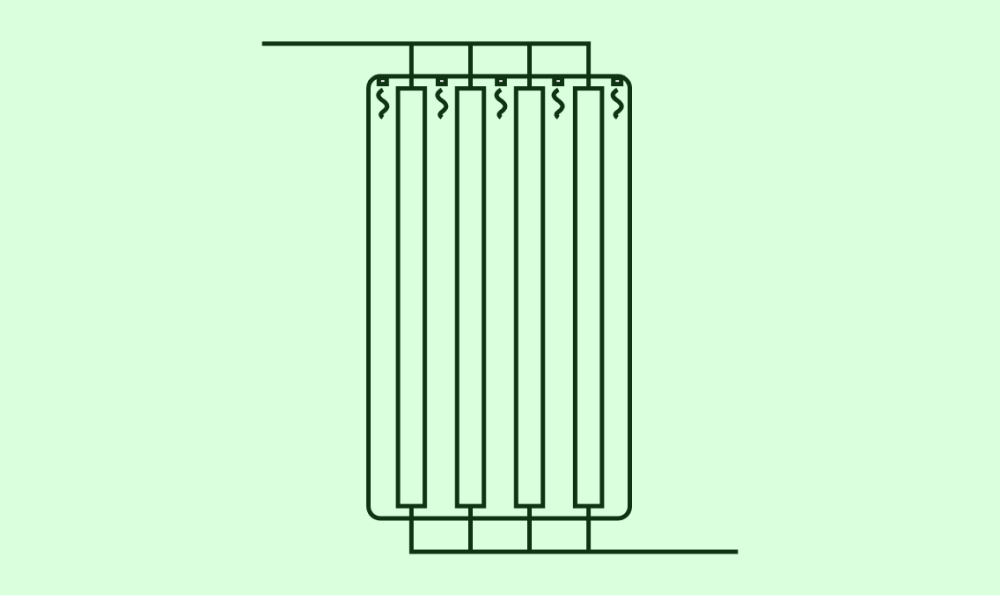
- Design similar to steam reforming
- Catalysts need high mechanical stability and low pressure drop
- Active metal coated / supported on carrier
- Pressure 20–40 bar / up to 700 °C
Clariant catalysts for fired tubular reactors
HyProGen 830 DCARB: Highly active and mechanically robust Nickel-based catalyst designed for high-temperature applications.
Our Catalysts
HyProGen™ 820 DCARB
Large-scale cracking Adiabatic reactor Catalyst
Nickel-based catalyst designed for high thermal stability, enabling higher inlet temperature to maximize conversion in adiabatic reactor
Product Benefits
- High thermal stability
- Active and robust catalyst
Customer Benefits
- Longer lifetime
- Higher conversion in adiabatic reactors
- Higher energy efficiency
HyProGen™ 821 DCARB
Large-scale cracking Adiabatic reactor Catalyst
HyProGen 821 DCARB is a highly active Nickel-based catalyst and an excellent alternative for Ruthenium catalyst with comparable stability and activity.
Product Benefits
- Highest activity close to Ruthenium
Customer Benefits
- Higher conversion in adiabatic reactors
- Higher energy efficiency
HyProGen™ 830 DCARB
Large-scale cracking Fired tubular reactor Catalyst
Nickel-based catalyst designed for high-temperature applications (550 – 750ºC) as in a reformer-type fired tubular reactor.
Product Benefits
- Well-proven with many references
- Excellent stability
- High activity
Customer Benefits
- Highest reliability and trustworthy
- Available in different shapes for tailor-made solutions
- Higher energy efficiency
HyProGen™ 850 DCARB
Precious metal catalyst for small-scale ammonia cracking
Highly active ruthenium-based catalyst designed for low-temperature and low-pressure applications (370 – 550°C)
Product Benefits
- High low-temperature activity
- High low-pressure activity
Customer Benefits
- Smaller and compact plant design
- Higher efficiency