How customers shape Clariant's next big innovations
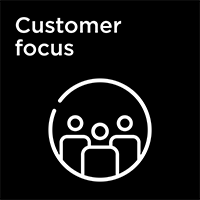
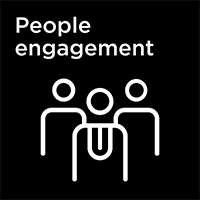
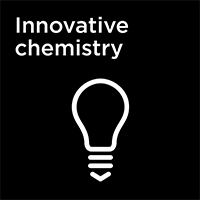
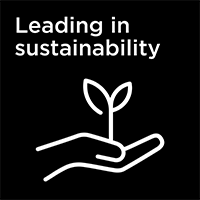
Delivering on Clariant's purpose »Greater chemistry - between people and planet.«
This story is an example of how Clariant delivers on its purpose-led strategy.
For a closer look at how Clariant delivers customer innovation in the petrochemicals industry, we spoke with Carlos Vianna, Global Product Manager-Ethylene. Carlos manages the portfolio of high-performance catalysts used in steam crackers for ethylene production, the key feedstock for making polyethylene. Carlos is a native of Brazil, a chemical engineer by training, and is based in The Woodlands, Texas.
Where does innovation start at Clariant Catalysts?
Carlos: Innovation springs from two key sources: customers and talented people. As a global leader in catalysts for over 70 years, our people have deep expertise across the board – catalysis, chemistry, R&D, engineering, production – we really know it inside out. But expertise alone doesn’t drive innovation. You need to collaborate and partner with customers to grasp their everyday challenges and how our products will better serve them. Many of us (including myself) are also former customers and plant engineers who have been in their shoes, so we have this invaluable insight into customers’ on-the-ground needs and pain points. By open communication and sharing knowledge, we set the ground to develop solutions. Even more important, we build trust to be the right partner to work with. And, as an independent catalyst supplier, Clariant can collaborate without competing with our customers in their markets. It’s this customer connection, combined with our teams’ technical know-how, that lays the foundation for innovation.
»The industry is undergoing major changes…and it’s driving innovation in production technology.«
Carlos Vianna, Global Product Manager-Ethylene at Clariant
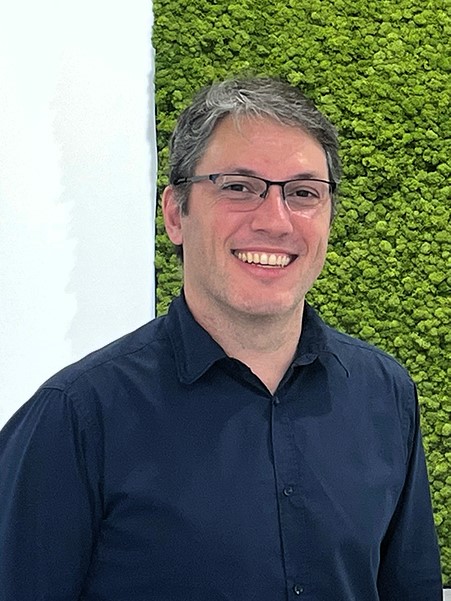
What emerging market trends are impacting the industry, and how can Clariant’s products help?
The industry is undergoing major changes--energy transition, low-carbon technologies, digitalization, electrification, end of plastic waste - and it’s driving innovation in production technology. Examples of a recent catalyst innovation in response to those trends is the new HDMax® products, an adaptable pyoil upgrading solution for chemical plastics recycling, transforming plastic waste into feedstock for steam crackers or OxyMax® E catalyst for low CO2 emission ethylene production. Though the landscape is changing, we see opportunity with our customers in developing novel solutions, turning obstacles into opportunities.What is one of Clariant’s most successful innovations?
We recognize sustainability as a priority for the industry. But Clariant stays focused on creating new chemistries to help to manage operational risks for customers, too. Keeping plants running safely and reliably is not flashy, but it remains vital work.
Our OleMax® 260 catalyst, launched in 2016, shows this commitment. As new ethylene plants are becoming more efficient, they need more advanced catalysts to achieve desired performance. OleMax 260 was developed specifically for these needs. Plants using OleMax 260 have seen impressive gains – much faster startups, stable and safer operations, and improved reliability, lower emissions. Customers are adopting it globally and fast. We see it as meaningful innovation leadership: Our goal has always been helping customers to operate soundly and productively. Clariant makes that possible through chemistry laser-focused on solving real challenges in today’s production environment. Colleagues in this industry say »OleMax 260 is one of the greatest catalyst developments ever«.
»Colleagues in this industry say ›OleMax® 260 is one of the greatest catalyst developments ever‹.«
Carlos Vianna, Global Product Manager-Ethylene at Clariant
How important is R&D and technical support?
People buy from people they trust. They want someone who isn't just going to ship product then disappear. They need constant technical and R&D support along the catalyst life. Therefore, rapid response, boots on the ground support, and on-site training is a must. With our global technical team and localized approach, Clariant can help customers faster. We support customers with frequent site visits to follow catalyst performance along the catalyst life (at loading, start up, reviewing operational procedures, technical evaluation) and we provide on-demand trainings and seminars. Also, our R&D group partners with universities and technical centers globally, which allows access to the latest technologies.
How do digitalization solutions help customers?
Clariant’s CLARITY™ – our service portal for catalyst customers – enables real-time data exchange and visualization of reactor performance. It is offered across all of Clariant catalyst applications and helps to optimize either plant or reactor efficiency, sustainability, and safety. Furthermore, if a customer needs technical support, our engineering team can easily review operating data and provide recommendations right away. CLARITY™ helps to process a huge amount of data and help customers make better decisions faster. Today, it has been adopted by more than 80 plants worldwide, serving more than 28 countries around the world.
»We support customers with frequent site visits to follow catalyst performance along the catalyst life and we provide on-demand trainings and seminars.«
Carlos Vianna, Global Product Manager-Ethylene at Clariant
What makes Clariant unique?
We’re listening to customers while leading with innovation. Customers know they need an experienced catalyst partner dedicated to their needs - and we deliver on that. But it’s more than that. We’re easy to work, nimble, and customer-focused and our company is truly focused on investing in innovation. We’ve strategically invested to become a far more responsive partner: Our digital capabilities help customers analyze challenges and make smarter decisions fast. R&D facilities and our tech experts can be deployed anywhere globally to respond to customer needs. And our Palo Alto high-throughput lab revolutionizes how rapidly we can develop new catalyst innovations tailored to customer applications.We’ve transformed processes to rapidly understand what customers require and deliver solutions tuned precisely to their needs. We pride ourselves on being an independent catalyst provider.
Can you give us an example?
Recently, a customer was having issues running one of their reactors and reached out to Clariant for help. We were able to figure out why and provide specific recommendations to improve it.We started by having daily calls to check on changes over the past 24 hours and discuss next steps. The situation became so stable and reliable that the customer could significantly increase how long the catalyst ran between cycles. This allowed them to avoid millions in production losses and reduce emissions.
As a result, this customer wants to keep working with us. Actually, it's more than that - they're sharing information about other catalyst needs where Clariant can definitely help. This shows our key Clariant value in action: winning with our customers.