Leveraging statistical data to revolutionize
a 60-year-old industrial catalyst recipe
Industrial phthalic anhydride (PA) catalysts play an integral role in manufacturing plasticizers used to make PVC plastics more flexible, durable, and easier to process. PA catalyst recipes have remained largely similar for the past 60 years, but new research from Clariant demonstrates the huge potential of optimizing these formulations through data-driven science. Leveraging statistical design of experiments (DoE) methodologies, Clariant scientists Oliver Richter and Gerhard Mestl uncovered opportunities for dramatic enhancements.
In a recent presentation at the 57th Annual Meeting of German Catalysis Researchers, they revealed how systematic DoE testing enabled step-change improvements to decades-old PA catalyst formulations by modelling interactive effects between promoters and compositions.
The oxidation process
PA catalysts are used to enable the oxidation process that converts o-xylene feedstocks into PA, an essential ingredient in plasticizers. This reaction occurs inside thousands of specialized tubes within industrial reactors, requiring a multi-layer catalyst system to balance activity and selectivity. Clariant’s patented OxyMax™ PA egg-shell catalyst comprises four to five distinct layers, each with tailored properties to account for the reaction’s complexity.
While various promoters have been reported to enhance VOx/TiO2-based PA catalysts, there had yet to be a systematic investigation of their synergistic effects. Clariant tackled this gap by utilizing statistical design of experiments (DoE) methodologies to efficiently screen parameter impacts and interactions with only a minimum number of tests.
Thwarting transport limitations
Initial experiments focused on identifying an optimal catalyst layer thickness that would eliminate pore diffusion limitations. This enabled intrinsic kinetic studies without mass transport influences skewing the data. Follow-on DoE testing examined the three most critical catalyst bed layers, mapping out mathematical models to predict promoter impacts on activity and selectivity.
The analysis found that vanadia content and cesium loading are the primary drivers of activity, contributing 70% of the model fit, while antimony and vanadium account for 80% of the selectivity response. Clariant leveraged these insights on promoter interplay to engineer superior formulations for each reactor position based on its required activity.
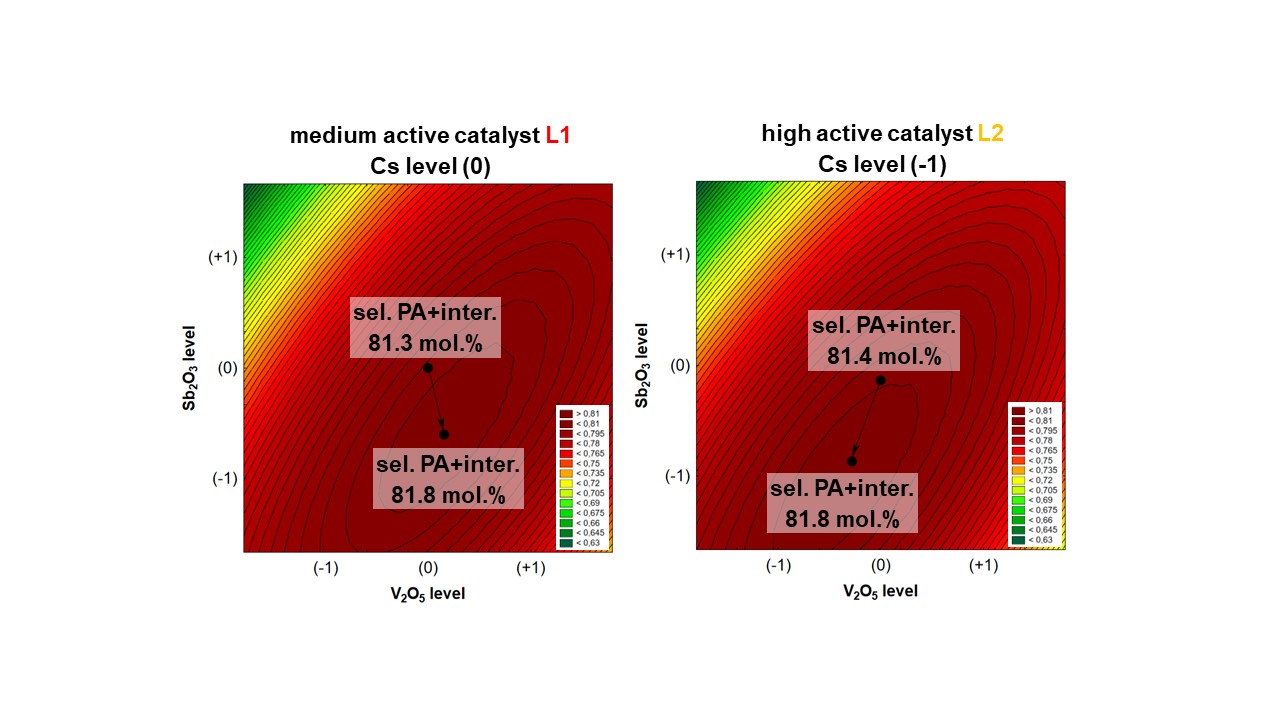
Demonstrating DoE’s potential
This DoE optimization strategy yielded a highly effective catalyst system, with performance exceeding previous benchmarks. By uncovering intricate effects between various catalyst components at different compositions, we proved the immense potential of embracing data-driven methodologies to enhance decades-old industrial processes.
Analysis revealed that key catalyst parameters control the majority of activity, but there are still "unknown effects" to explore. As computational capabilities continue improving, combining statistical DoE screening with kinetic modelling and machine learning prediction holds promise for further advancing catalyst development.
Leveraging DoE learnings across entire catalyst architectures could lead to even higher selectivity and activity levels in next-generation systems. Data-driven DoE methods demonstrate immense potential to continually improve industrial catalysts.
Driving sustainable impact
Beyond enhancing process economics, these innovations also promote sustainability by boosting energy efficiency and reducing waste. With Clariant catalysts enabling increased PA production from fewer raw material inputs, the minimized environmental footprint will help the industry achieve ambitious decarbonization goals.
And by revealing the potential of rethinking decades-old assumed “recipes,” this research motivates fresh perspectives in other applications too. There are likely more opportunities to incorporate statistical DoE workflows for reinventing products, substituting inputs, and boosting quality across Clariant’s portfolio.
This blog post is based on the scientific session "Statistical Data Driven Research Strategy: A Key to Improve the 60-Year-old Recipe of Industrial Phthalic Anhydride Catalysts " presented by Dr. Oliver Richter on March 15th 2024, at the 57th Annual Meeting of German Catalysis Researchers in Weimar, Germany.
Oliver Richter earned his doctorate in Chemical Engineering from the Karlsruhe Institute of Technology. He currently leads R&D efforts in Oxidation Catalysis, developing innovative selective oxidation catalysts that enable sustainable production processes across chemical, polymer, food, and pharmaceutical industries. His decade-plus career has advanced the field of heterogeneous catalysis through numerous patents and publications.