Uncovering overlooked opportunities in ethylene production
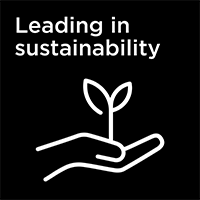
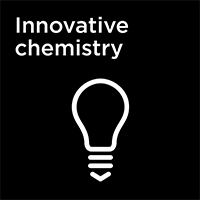
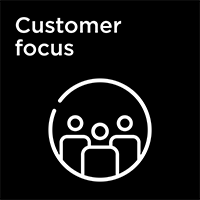
Delivering on Clariant's purpose »Greater chemistry - between people and planet.«
This story is an example of how Clariant delivers on its purpose-led strategy.
The interview focuses on how Clariant helps ethylene producers address overlooked opportunities in acetylene conversion, with emphasis on sustainability, efficiency, and specialized technical expertise. Francisco Amaral discusses specific catalyst solutions, including OleMax 207 and OleMax 260, and how Clariant's customer-centric approach helps uncover hidden efficiency opportunities.
Francisco Amaral, Technical Advisor for Olefins Production at Clariant Catalysts, recently sat down with Kristina Morgan, Global Marketing Manager, Petrochemicals at Clariant, to discuss how we’re responding to customer needs in the changing ethylene industry landscape.
Welcome, Francisco. Here at Clariant, customer focus, sustainability, and innovative chemistry form the foundation of everything we do. In your role as Technical Advisor for Olefins Production for BU Catalysts, you're on the front lines with our customers every day. How do you see these core values helping them address the complex challenges they're currently facing?
Ethylene producers face unprecedented challenges, Kristina. While decarbonization remains critical long-term, our customers are also dealing with volatile feedstock prices, geopolitical tensions, and global overcapacity. By keeping their needs central to our innovation, we're helping them maintain competitiveness, despite these pressures.
How does our approach influence the catalyst solutions we develop for ethylene producers?
We've recognized that while ethylene producers typically focus on major equipment like pyrolysis heaters and compressors, catalysis plays a pivotal yet often overlooked role. The furnaces and major equipment that receive most attention represent the higher energy consumption in the plant and therefore, also generate the majority of CO2 emissions. Plant engineers naturally focus there. However, significant efficiency savings exist in acetylene reactors-but these opportunities can be overlooked.
Why are these opportunities overlooked?
Catalysis is a highly specialized and technical field all on its own, often not taught comprehensively in engineering schools. Plant operators are focused on running complex operations day-to-day, and frequently they don’t have the time-or specialized knowledge-to identify and solve these issues! And that's exactly where Clariant Catalysts' technical expertise becomes invaluable.
Acetylene converters stand as one of the most sophisticated reactor systems in the ethylene production process. Consider the challenge: completely eliminating acetylene from a stream rich in ethylene-your primary product-while minimizing its hydrogenation to ethane. This operation requires precise conditions; insufficient catalyst activity prevents reaching product specifications, while excessive activity not only destroys valuable ethylene, but also could trigger dangerous temperature excursions within the reactor. Such complexity demands both superior catalyst technology and operational expertise, areas where Clariant demonstrates exceptional capability. Our combination of advanced catalytic solutions and specialized process knowledge ensures these critical systems operate safely, efficiently, and with optimal selectivity.
Could you explain how our innovative chemistry addresses these often-overlooked challenges in acetylene conversion?
We've developed specialized catalysts for both front-end and tail-end hydrogenation reactors by understanding their distinct challenges-whether managing catalyst formulation to improve the stability of the product to avoid runaway events in front-end systems or addressing green-oil formation and increasing the selectivity in tail-end setups. Either front-end or tail-end acetylene converters directly impact two critical aspects of operations: reliability and selectivity. Both have significant implications for sustainability and efficiency.
How specifically do our solutions contribute to sustainability goals in these overlooked areas?
When an acetylene converter fails to meet specifications, the reactor effluent often goes to flare, resulting in production losses and significant CO2 emissions. Our catalysts are designed to maintain specifications even during plant variations and upsets, dramatically reducing these environmental impacts.
Additionally, high selectivity that can be obtained with our catalysts improves ethylene yield while reducing energy consumption. Transforming acetylene into the desired product rather than ethane minimizes recycling loads from the cold fractionation section to the furnaces, reducing energy costs and emissions. For capacity-limited plants, this means higher ethylene production from the same feedstock. These opportunities often remain unseen, and we're helping customers achieve sustainability gains with the Acetylene converters, they might not have known were possible.
"We don’t just provide products-we share our specialized knowledge in catalysis, helping customers discover sustainability and efficiency opportunities that might not be top of mind."
Francisco Amaral
Technical Advisor for Olefins Production
Catalysts
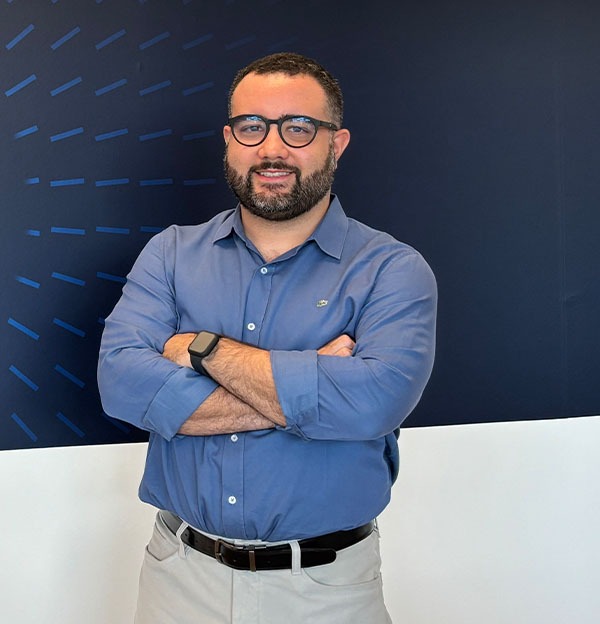
Can you highlight specific products that exemplify our commitment to sustainable innovation?
OleMax 207 demonstrates this commitment for tail-end configurations. Its exceptional stability allows operators to run acetylene converters continuously through entire Steam Cracker campaigns, potentially eliminating regeneration for years. This translates directly into energy savings, minimized effluent generation, and lower CO2 emissions.
Customers who previously experienced approximately one-year cycle runs in their tail-end units with earlier generation catalysts are now achieving three, four, or even longer operational cycles. This extended performance reduces regeneration frequency throughout the catalyst lifecycle and depending on process configuration and spent catalyst management protocols, may potentially eliminate regeneration requirements entirely in these systems. For front-end operators, OleMax 260 is a game-changer. It was a catalyst specifically invented to nearly eliminate runaway events during fluctuations and upsets, thanks to its unprecedented selectivity. Customers report it achieves specification faster and requires fewer conditioning steps before startup, significantly reducing flare time and emissions during critical phases. We’ve calculated that 1 flare event equals about ~3,000 tonnes of CO2 avoided in a 24-hr. flare event in a world-scale plant.*
How does our service approach reflect our customer-centric philosophy?
Our Applied Catalyst Technology (ACT) team provides crucial support that maximizes performance and ensures reliability. This team serves as an extension of our customers' technical capabilities. We've designed our selective hydrogenation portfolio to work across diverse process schemes from all major licensors. Our global technical team provides application training, reactor performance optimization, and troubleshooting-all tailored to each customer's specific needs. This personalized support has become a key differentiator for Clariant. While these opportunities for improvement often remain hidden within the "black box" of catalysis, we can demystify this specialized field, while also helping customers achieve efficiency and sustainability gains, they might not have known were possible.
How does CLARITY enhance our customer-centric approach while supporting sustainability goals?
CLARITY enables customers to share data more rapidly, allowing our ACT team to provide faster, more targeted support. The standardized metrics help us deliver richer recommendations that address each customer's unique challenges. What's valuable about CLARITY is how it provides clear, actionable insights that empower customers to make more informed operational decisions. Its ability to predict off-spec events helps prevent flaring and emissions. The comprehensive history line for each reactor improves knowledge retention and transfer, ensuring optimal performance even as personnel changes. Our ethylene team is developing a premium version with additional features to further enhance reactor performance and predictive capabilities-innovations driven directly by customer feedback.
How does strengthening customer relationships contribute to our innovation pipeline and sustainability goals?
Our collaborative approach with customers drives our innovation strategy. By working closely with them, we gain invaluable insights that inform our product development. This customer-centric cycle helps us build expertise around critical operational units like acetylene converters, directly impacting sustainability through improved efficiency. What's unique is that we don't just provide products-we share our specialized knowledge in catalysis, helping customers discover sustainability and efficiency opportunities that might not be top of mind. Indeed, these interactions frequently serve as valuable learning opportunities for us as well. As we continue to expand our knowledge base and accumulate experience, we strengthen our ability to provide increasingly sophisticated expertise and tailored solutions to our customers. I'm proud that at Clariant's Catalyst Business Unit, we're meeting industry challenges with exceptional products and a talented global team equipped with the right tools to support our customers. Our focus positions us as true partners in our customers' success.
It's clear how Clariant's dedication to our core values translates into practical solutions that make a real difference in the chemical industry. By applying our specialized catalysis expertise to these often-overlooked areas, we're uncovering opportunities that might otherwise remain hidden. Thank you for these insights.
Thank you, Kristina. I'm excited to continue this journey with our customers and the entire Clariant team.
Based on Clariant internal calculations and “The Impact, the opportunity: How catalysts drive the net-zero transition,” by Wolf Spaether and Carlos Vianna, 2022.
More greater stories
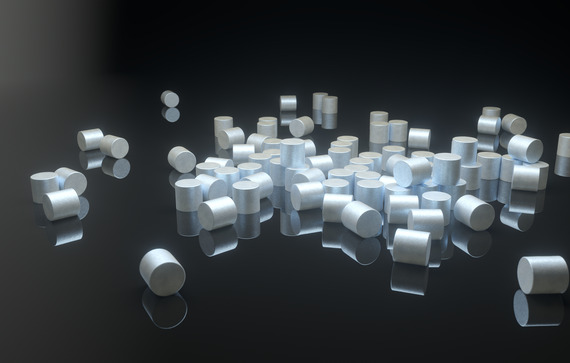