Recycling plastics
with fire
In classical mythology, fire is a gift to humanity from the gods. In our present day and age, it may help us solve our problems with plastic waste. Bettina Siggelkow, EcoCircle Program Manager at Clariant, tells us about the fascinating new recycling technology of pyrolysis, and how Clariant contributes to making it work.
Ms. Siggelkow, we all know that pyrotechnics have to do with fireworks. But what does pyrolysis mean?
»Pyro« comes from the ancient Greek word for fire, and combined with »lysis« it means »dissolving with fire«. Pyrolysis is actually a quite old chemical method. But it’s now being used to convert plastic waste under high heat into so-called pyrolysis oil, which is similar to crude oil.
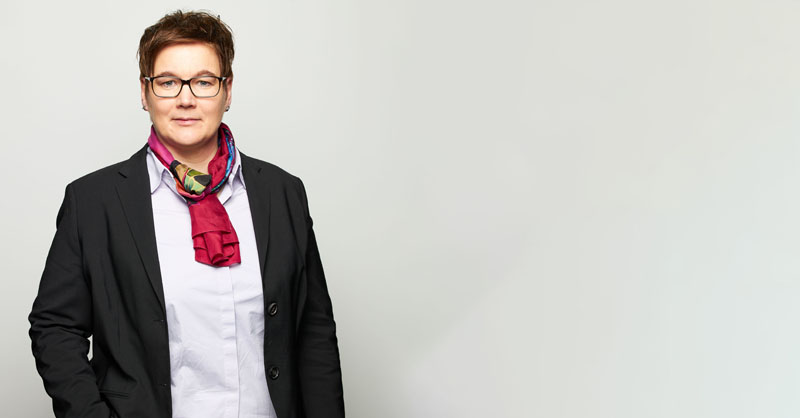
Why has this fiery old technology become such a hot new topic in plastics recycling?Because the recycled raw plastic obtained with classical mechanical recycling can’t be used for everything. Impurities from other plastics in the waste, can make it unfit for use in food packaging or drinking bottles, for instance. Also, due to the damage reprocessing does to the polymers plastics consist of, they can’t be recycled with this method more than approx. five times.
What’s different when using pyrolysis?
The difference is that the oil it yields can be split into monomers just like crude oil. These chemical building blocks can then be turned into new polymers and plastics that are exactly like those made from virgin feedstock, without any impurities or processing damage. Theoretically, this means pyrolysis could be used to create an endless recycling loop.
That sounds very promising. What kind of plastic waste can this method be used for?
That’s the second reason for the new popularity of pyrolysis. While it isn’t true that it’s suitable for all plastic types, it’s easier to use with mixed plastic waste, or with multilayered materials like those used in food packaging. There still has to be some sorting, to weed out plastics affecting the purity of the pyrolysis oil. But overall, it’s a great complementary method for breaking down plastics currently left unrecycled but incinerated or landfilled, trapping contaminants in side products, and ending up with fresh polymer.
»In principle, pyrolysis can greatly contribute to decarbonizing our economies – by not feeding plastics production with fossil resources but instead with oil extracted from plastics, so to say.«
How widely is pyrolysis used presently?
There are many companies looking into it in pilot plants, but it’s not yet being used on a grand commercial scale. One big research challenge is the amount of energy required, which is critical for pyrolysis to be beneficial compared to conventionally produced oil or incineration. But in principle, pyrolysis can greatly contribute to decarbonizing our economies – by not feeding plastics production with fossil resources but instead with oil extracted from plastics, so to say.
Where does Clariant come in? What contribution can we make to the success of this new method?
As I mentioned, the quality of the pyrolysis oil is very important. Only sufficiently decontaminated oil is fit for cracking it like crude oil and converting it to new chemicals and plastics. Impure oil tends to be simply used as fuel. This still prevents the plastic waste which it is based on from being landfilled, but is inferior in terms of circularity.
So we can help to make the oil more pure?
Exactly. We have identified a technology that removes critical components, like chlorides, bromines and metals. Black pyrolysis oil goes in, orange or light yellow oil comes out. This is mainly due to the discolorations removed, but it provides a good idea of how our technology works. And this isn’t our only solution for supporting the process.
What other solutions do we have?
If the oil is not produced near a cracking plant, it needs to be transported and stored. However, unsaturated compounds in the oil often take this as an opportunity to »hook up« with each other and create unwanted polymers. These make the oil more viscous, leading to waxy deposits, clogging of pumps, and other issues.
And we have a way of preventing these undesired activities?
Yes, we do. In fact, our »hydroprocessing« catalysts are genuine experts in keeping oil thin and easy to handle. We have used the next-generation HYDEX™ E catalyst to help one of our partners turn pyrolysis oil made from plastic waste into high-quality winter diesel, which doesn’t clog – even at arctic temperatures. And given the popularity of pyrolysis, it’s only a question of time until our catalysts will be turned to a fully circular purpose.