Spotlight on Louisville
TAKE A PEEK INSIDE OUR CONNECTED AND DIGITALIZED POLYPROPYLENE CATALYST PLANT
Clariant Catalysts and Lummus Technology’s joint polypropylene catalyst production plant in Louisville, Kentucky, was officially inaugurated on October 17, 2016. Today, it is Clariant’s largest catalyst production site in North America and equipped with state-of-the-art systems that enable fully automated and digitalized operations. For a closer look at the technology and its effect on day-to-day processes, we spoke to Wendell Borges, Production Manager of the Louisville polypropylene catalyst plant.

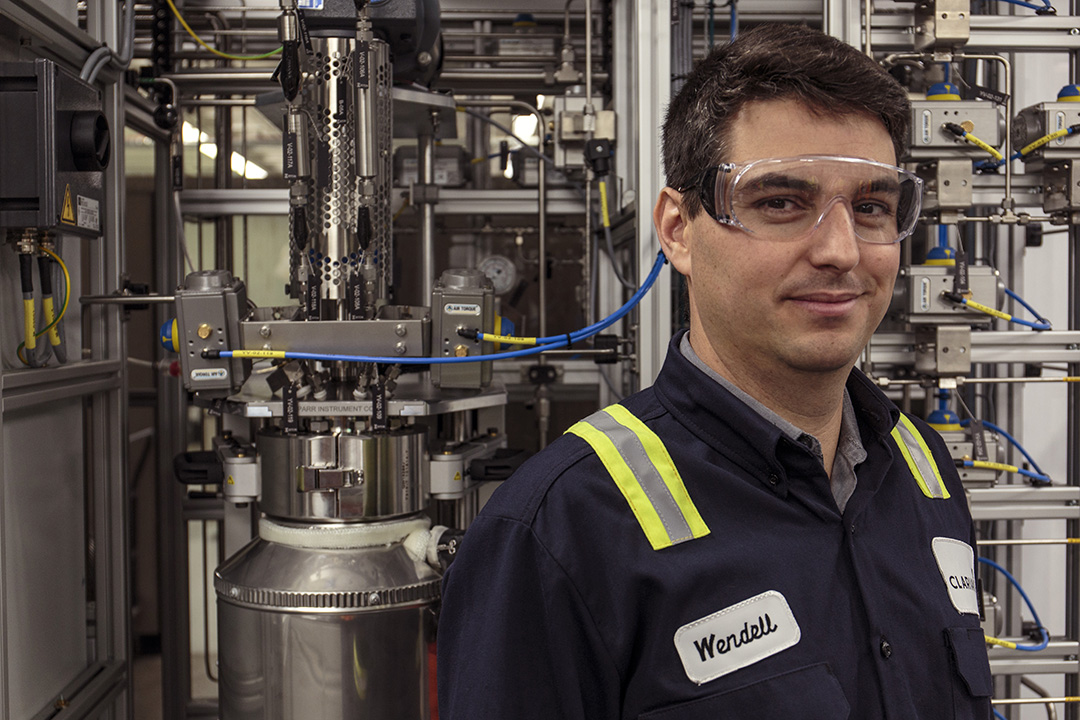
… we are capable of producing polypropylene catalysts for a large variety of processes... «
Can you start with an overview of the products you manufacture at the plant?
WB: Due to the plant’s advanced technologies, we are capable of producing a broad portfolio of polypropylene (PP) catalysts. One example is the NHP™ Catalyst made exclusively for Lummus Technology’s highly versatile, reliable, and cost-efficient Novolen™ process for the production of an entire range of PP resins. We also make Clariant’s high-performance PolyMax™ Series catalysts, which are formulated for a wide variety of different PP process technologies.
Can you start with an overview of the products you manufacture at the plant?
WB: Due to the plant’s advanced technologies, we are capable of producing a broad portfolio of polypropylene (PP) catalysts. One example is the NHP™ Catalyst made exclusively for Lummus Technology’s highly versatile, reliable, and cost-efficient Novolen™ process for the production of an entire range of PP resins. We also make Clariant’s high-performance PolyMax™ Series catalysts, which are formulated for a wide variety of different PP process technologies.
What is digitalization, and how does it benefit your plant operations?
WB: Before discussing digitalization, it is important to point out that it all starts with automation. We have removed manual steps and standardized processes in all areas, which dictate when products are run, how materials are selected, and where to produce. This reduces the burden on our operators who can more effectively manage plant activities.
The next layer is digitalization. Our system provides remote access to virtually every aspect of the plant. A multitude of tools collect, report and allow management of detailed features, such as consumption, utilities, raw materials, reactor temperatures, equipment performance and quality data – all within seconds. All of this information is sent to a global data pool, which is processed and combined into dashboards, so we have access to fast, fresh data on any mobile device in just a few clicks.
How does it affect the production and development of new catalysts?
WB: All of this digital information is saved into a data pool, which enables detailed troubleshooting and optimization. For instance, by comparing a new production batch to the internal standard, we are able to assess and amend any deviations. Overall, digitalization leads to higher quality products while improving accuracy and boosting productivity.
Besides enhancing the manufacturing of current products, the system is also invaluable for developing or producing new catalyst series. The wealth of data collected from previous process experiences allows advanced statistical analyses and correlations to create the optimal catalyst morphology and particle size for each application, thereby drastically shortening new product launches.
Is digitalization unique in the industry?
WB: Although digitalization is becoming more common in other industries, it is not often applied to chemical production, since older plants mainly run manual processes. This truly makes the Louisville PP catalyst plant so unique.
How does it help with personnel safety and process security?
WB: Automated reports are generated on a daily basis, giving our team a clear, extremely detailed picture of the entire production process. This not only allows easier enhancements and modifications, but also ensures operational safety in the event of equipment failure and maintenance requirements. The data allows us to forecast if there might be a problem in the near future, so we can detect, diagnose and correct potential troubles – before they occur.
Has digitalization changed your work culture?
WB: No degree of technology can fully replace human interaction, management, and supervision. That’s why the plant relies on experienced operators and shift leaders as well as engineering and maintenance teams. Digitalization has made us more connected, less siloed. We’ve improved communications, enhanced our work culture, and streamlined efforts, as our staff has unfiltered access to accurate product information – and nothing is lost in translation.
How is your plant managing the current pandemic?
WB: Initially, we were quite concerned about going into lockdown and halting production; it was a situation that we’d never encountered before. Thanks to our extensive digital tools, we quickly realized that it was possible to use the troubleshooting technology to support our operators and sustain production. It doesn’t substitute having our team present, but it allows us to protect all our employees during the pandemic and continue making top quality catalyst.
Novolen™ and NHP™ are registered trademarks of Lummus Novolen Technology GmbH.