Tackling greenhouse gas emissions, one handprint at a time

Human hands have 27 bones, 29 joints, and at least 123 named ligaments. What sets our hands apart from other animals is our opposable thumbs – meaning our thumbs and fingers can work together. The human handprint has been, throughout history, the visual mark that says “I was here” – spanning from Paleolithic times with negative prints in caves, up until today with the use of biometric technology at airports.
With businesses aiming to become climate-neutral, the term carbon handprint was coined to designate actions that leave a positive mark to reduce greenhouse gas emissions. In contrast to the more well-known term carbon footprint1, the carbon handprint2 refers to the positive environmental impacts that organizations make by providing products that reduce the footprints through a product or service life cycle, in relation to a reference alternative solution.
Clariant offers innovations to help reduce the greenhouse gas (GHG) emissions of chemical companies. Central to the modern world economy, the chemical industry accounts for up to 6% of GHG emissions3: “The equivalent of 1.9 billion tons of CO₂ is emitted globally from chemical operations every year," says Marvin Estenfelder, Global Head of Research & Development at Clariant Catalysts. "Close to half of these emissions stem from the production of just four chemicals – ammonia, ethylene, propylene, and methanol. At Clariant, we have solutions for all of them and more."
Clariant’s wide range of specialized catalysts not only makes the chemical production process safer, easier, and faster—what’s more, they help the environment by reducing greenhouse gas emissions. Let’s take a closer look at four examples of four different solutions.
From "no catalyst" to "now catalyst"
To cut its customers’ greenhouse gas emissions, Clariant incentivizes catalytic off-gas purification in production plants that previously ran without it. An example includes the production of nitric acid, an essential compound for making the kind of fertilizers that ensure reliable harvests for the world’s growing populations. There are about 500 nitric acid plants operating around the world – combined, they produce more greenhouse gases than 21 million cars per year4. The emissions come in the form of nitrous oxide (N₂O), which is about 300 times more harmful to the climate than carbon dioxide (CO₂)5. To help nitric acid companies cut their nitrous oxide emissions, Clariant developed EnviCat™ N₂O-S, a catalyst that can easily be ‘dropped’ in most nitric acid production factories, which is able to convert up to 95% of the nitrous oxide into harmless oxygen and nitrogen.
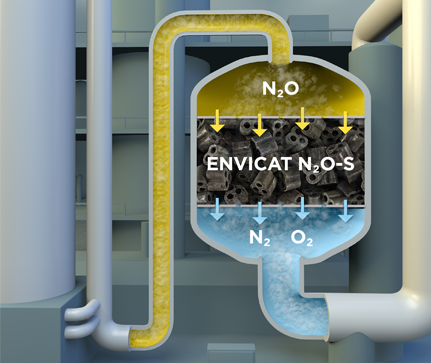
EnviCat™ N₂O-S converts N₂O formed during nitric acid production into harmless oxygen (O₂) and nitrogen (N₂). ©Clariant
From good to excellent catalysts
Through constant innovation, Clariant develops next-generation catalysts that enable customers to easily opt out of previous solutions at their production plants. "Our drop-in solutions increase productivity and energy savings without much additional investment or engineering needed," says Estenfelder. An example includes AmoMax™ 10 Plus for the production of ammonia – a compound that today is mainly used to produce chemical fertilizers but additionally could be utilized in the future as a carrier to facilitate hydrogen transport and as emission-free fuel in fuel cells and turbines. Clariant’s catalyst not only increases ammonia output but is also particularly robust. For a typical ammonia plant the catalyst reduces CO₂ emissions by up to 100,000 tons over the catalyst lifetime—15 years—compared to its predecessor catalyst6.
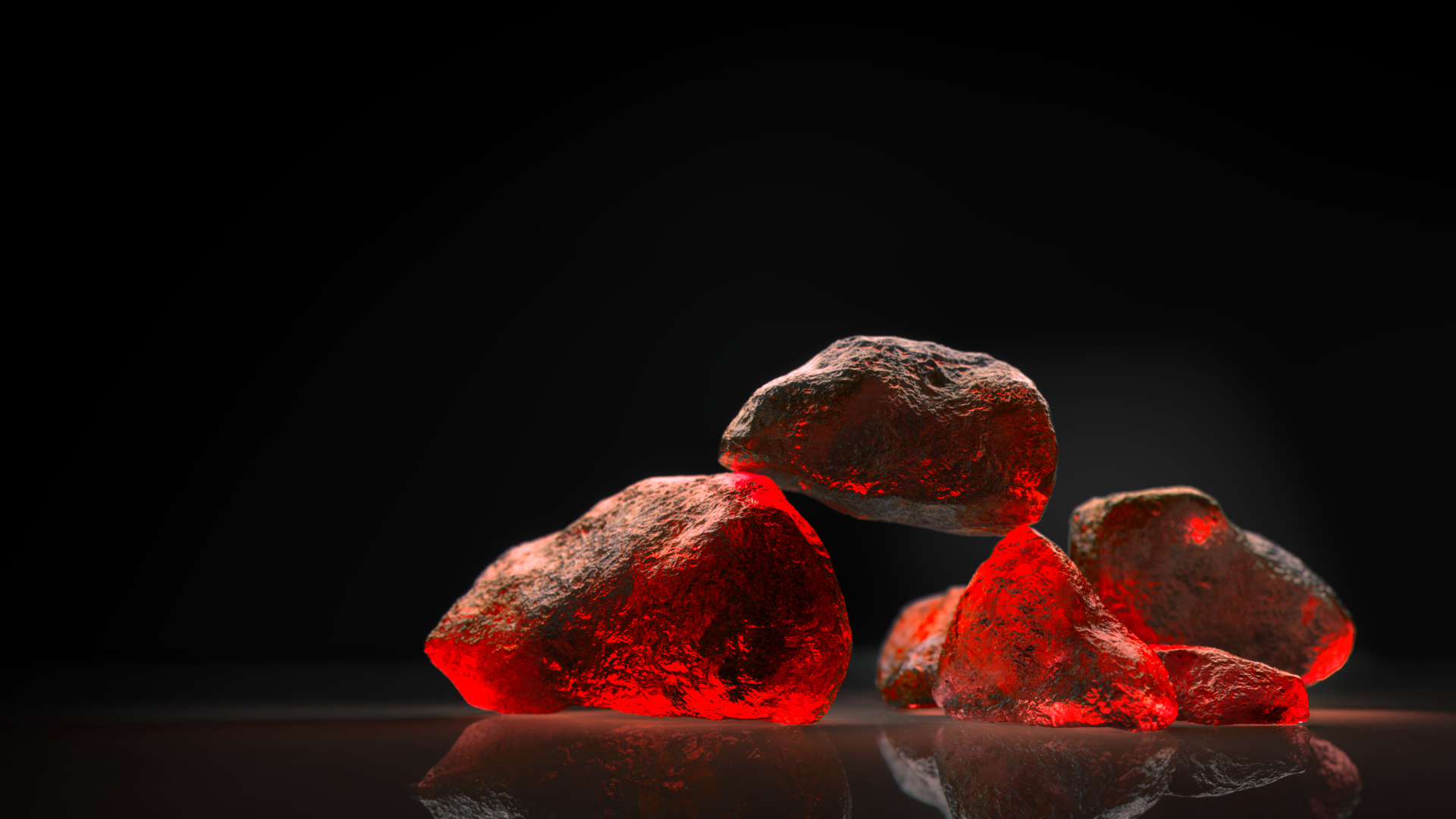
AmoMax™ 10 Plus: ammonia synthesis catalyst boosts production while reducing CO₂ emissions. ©Clariant
From process-to-process breakthrough
Another groundbreaking technology co-developed by Clariant could help kickstart the hydrogen economy. An increasing number of countries globally are investing in hydrogen as a potential climate-neutral energy carrier to wean their economies off fossil fuels. Yet, today's hydrogen production is still carbon intensive. "99% of all hydrogen is produced from fossil resources, mostly methane," says Estenfelder. The process, called steam-methane reforming, produces around ten tons of CO₂ for every ton of hydrogen. Developed by Clariant and Technip Energies, a leading engineering company in the energy section, EARTH™ (Enhanced Annular Reforming Tube for Hydrogen) is a breakthrough in more sustainable hydrogen production. The technology consists of a novel catalyst integrated into a new tube-in-tube system that can be installed straight into the tubes of most current steam reformers. The first plant to use it reduced its fuel consumption by almost 40% and its CO₂ emissions by 20%.
From evolution to revolution
Then, there are innovations where catalysis could help revolutionize entire industries – one example being ethylene. With over 200 million tons produced annually, ethylene is one of the most widely produced petrochemicals as it is the essential building block for making resins and plastics. Yet, the production process is energy intensive and, alone, accounts for 9%7 of total greenhouse gas emissions emitted by the chemical industry. As an innovative solution, Clariant and Linde Engineering jointly developed a groundbreaking catalyst that allows for the oxidative dehydrogenation of ethane (ODH-E) into ethylene, which eliminates the need for steam-cracking furnaces. The low-emissions catalytic technology could reduce between 40-60% of CO₂ emissions, and up to 100% if the system is run on renewable resources, versus traditional ethylene production via steam cracking. "Our solution is the first to make ODH-E commercially viable, marking a sea-change for one of our industry's most carbon-intensive sectors," explains Estenfelder.
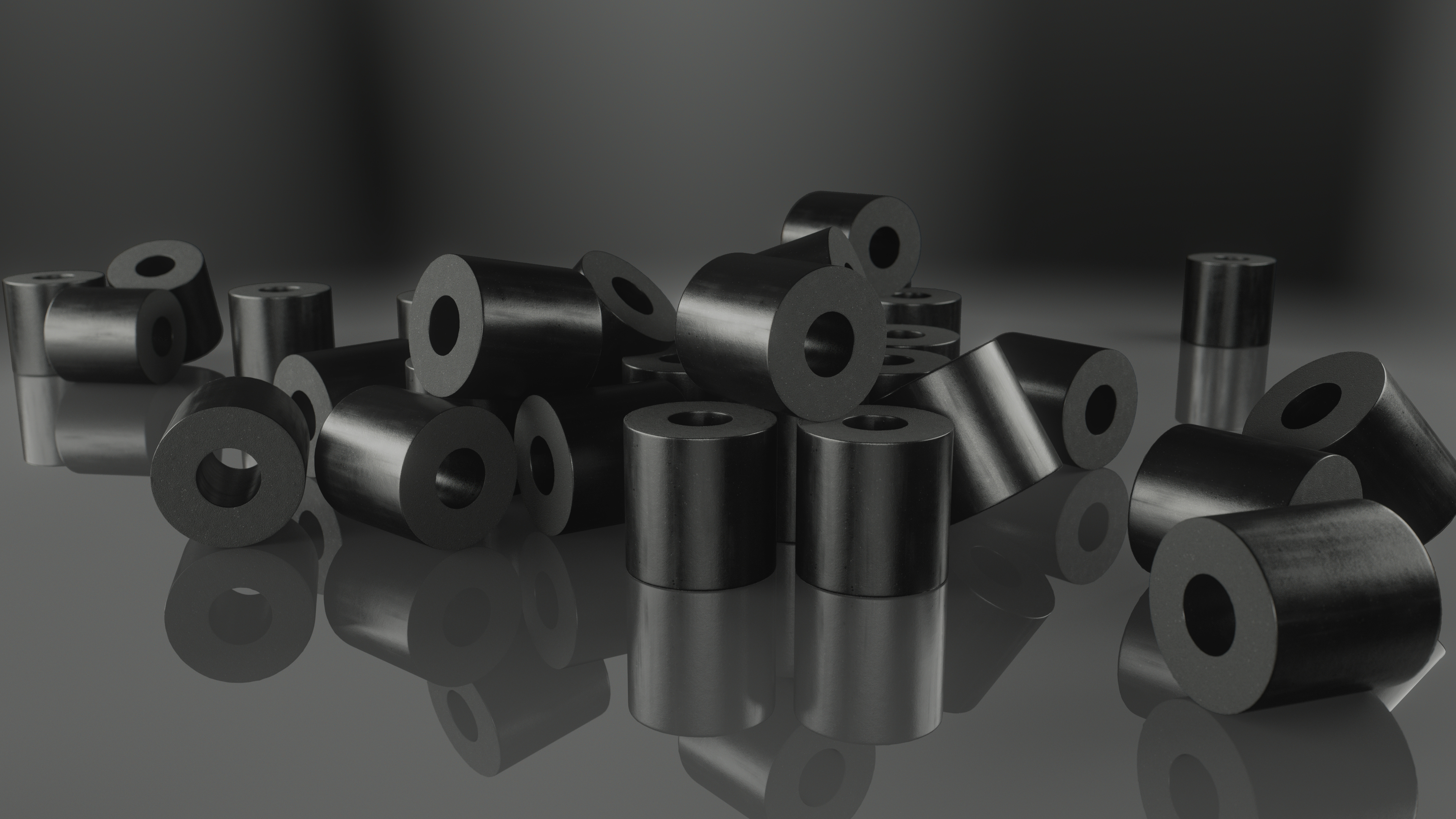
Linde’s EDHOXTM plant uses the groundbreaking new ODH catalyst. ©Clariant
The examples discussed show how Clariant’s catalysts are at the heart of chemical processes that drive sustainability. The design of novel catalytic materials and technologies can not only improve production efficiency but also tackle global challenges to leave a positive handprint2 across the chemical industry.
[1] The carbon footprint refers to the sum of GHG emissions and GHG removals in a product’s life cycle, expressed as CO₂ equivalents.
[2] In this article, the reference to handprint does not cover the full life cycle, and the key assumption is that all other life cycle steps beyond the catalyst use are the same in relation to the reference alternative solution.
[3] Bloomberg, “Many global chemicals companies trail on carbon-transition goals”, 27 January 2021.
[4] Annually, N₂O emissions from the production of nitric acid and its derivative adipic acid is equivalent to about 100 million tons of CO₂. Source: IPCC Fifth Assessment Report, “Climate Change 2014”
[5] United States Environmental Protection Agency, “Overview of Greenhouse Gases”
[6] Based on a 1,600 mtpd plant
[7] IEA, “The Future of Petrochemicals”, 2018