800 volts under the driver's seat
How safe can high-voltage e-mobility be?
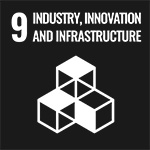
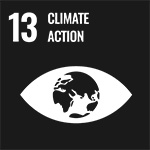
Our contribution to the SDGs
The new mobility also requires a new infrastructure, both for its production and for its application. All this must change mobility - travel and transport in the future can become climate-neutral. So, this story is a contribution to the SDGs 9 and 13.
The challenge
Electromobility is on the rise. High-performance batteries are becoming more and more powerful and bringing higher voltages to more and more cars. This not only reduces direct CO2 emissions, but also increases the risk of fire. Instead of a normal 12 volts battery in conventional cars, all-electric vehicles have fast-charging cycles that can involve 800 volts or more. These can cause short-circuits and sparks that can ignite flammable materials. There are also significant differences in use. While the conventional car sleeps at night, so to speak, the electric car charges, practically unattended. This makes fire safety one of the central challenges in building mass-market electric vehicles.
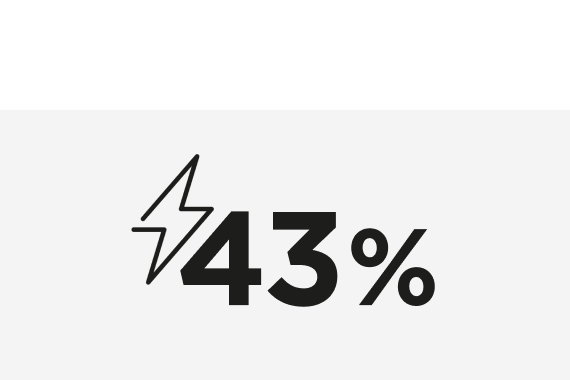
more electric vehicles on the roads from 2019 to 2020
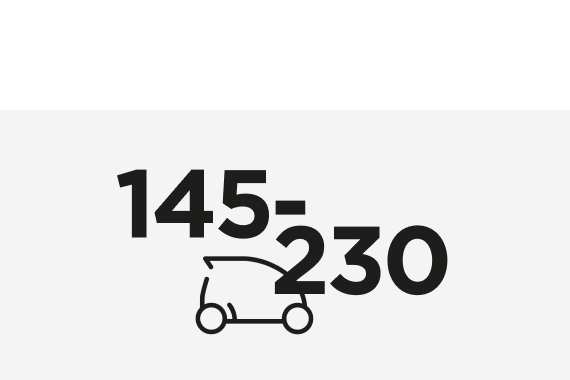
more electric vehicles projected by the end of this decade
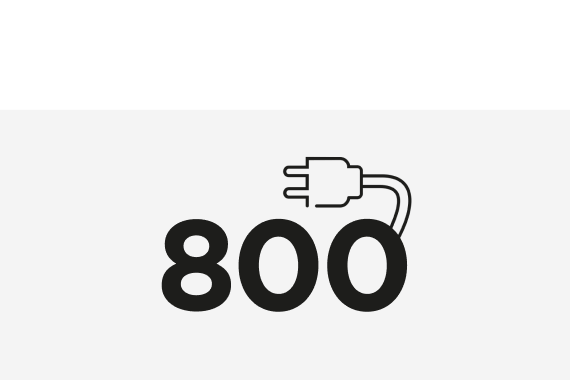
volts fast charging cycles in more and more all-electric vehicles
The need
Car manufacturers of electric cars have two main factors in mind. One is reducing weight to extend the range and the other is reducing cost to be competitive with combustion engine cars. All the electronics influence both immensely. Higher voltages are now also putting more and more focus on high performance polymers and flame retardants. Clariant has been collaborating with customers and further along the value chain: we have found solutions for high voltage connectors to address shifting technical requirements needed for e-mobility systems, enabling the use of flame retarded polyamides and polyesters in such connectors, around batteries and in charging infrastructure.
»We see some of the highest voltages and currents precisely as the car is unattended.«
Sebastian Hoerold
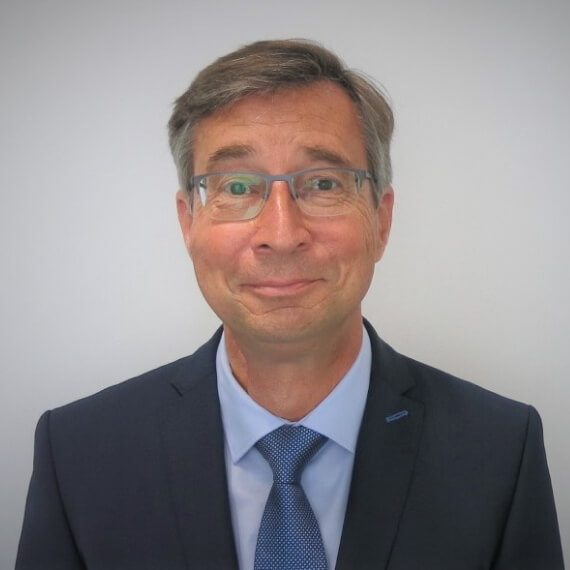
The solution
Clariant's Exolit™ has been in use for two decades in some of the most demanding industries, from smart consumer electronics to home appliances to industrial applications. Based on organic phosphorus compounds, Exolit™ can stop plastics burning within seconds and thus stop flames from spreading. It also helps minimize the risk of creepage and sparks. Exolit™ is non-halogenated, which makes it safer and more environmentally compatible than most solutions out there. Most flame retardants make plastics more brittle, less workable, and even less durable overall. Some make specific production processes harder or even impossible. Exolit™ flame retarded polyamides and polyesters can address the carmakers demands on performance, safety and sustainability. Clariant expands its capacity for Exolit OP following the demand in e-mobility. In addition, Exolit is a preferred choice for composite materials, flexible printed circuit boards and adhesives used in electric vehicles.
Investing in the future
This story is not over yet. We are building a new state of the art facility for Exolit in China. This is close to the large Chinese market and can logistically cover many other locations. Regional and global supply will work more closely with our customers to fulfill increasing safety regulations and technical performance requirements. We are commencing production in Dayabay around mid-2023, with the second line due to come on stream within 2024.
What makes this chemistry greater?
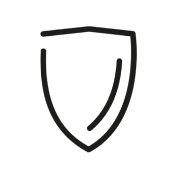
Safer e-mobility:
Exolit provides effective protection of easily flammable materials in case of short circuits.
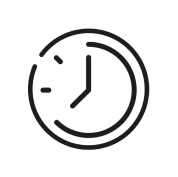
Less brittle, more workable:
Exolit enables carmakers to work with engineering plastics without compromising on mechanical properties or durability.
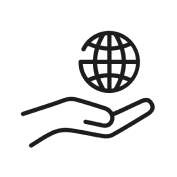
More sustainable:
Exolit is halogen-free with an excellent environmental and health profile.