Can biomass waste improve manufacturing efficiencies and circularity?
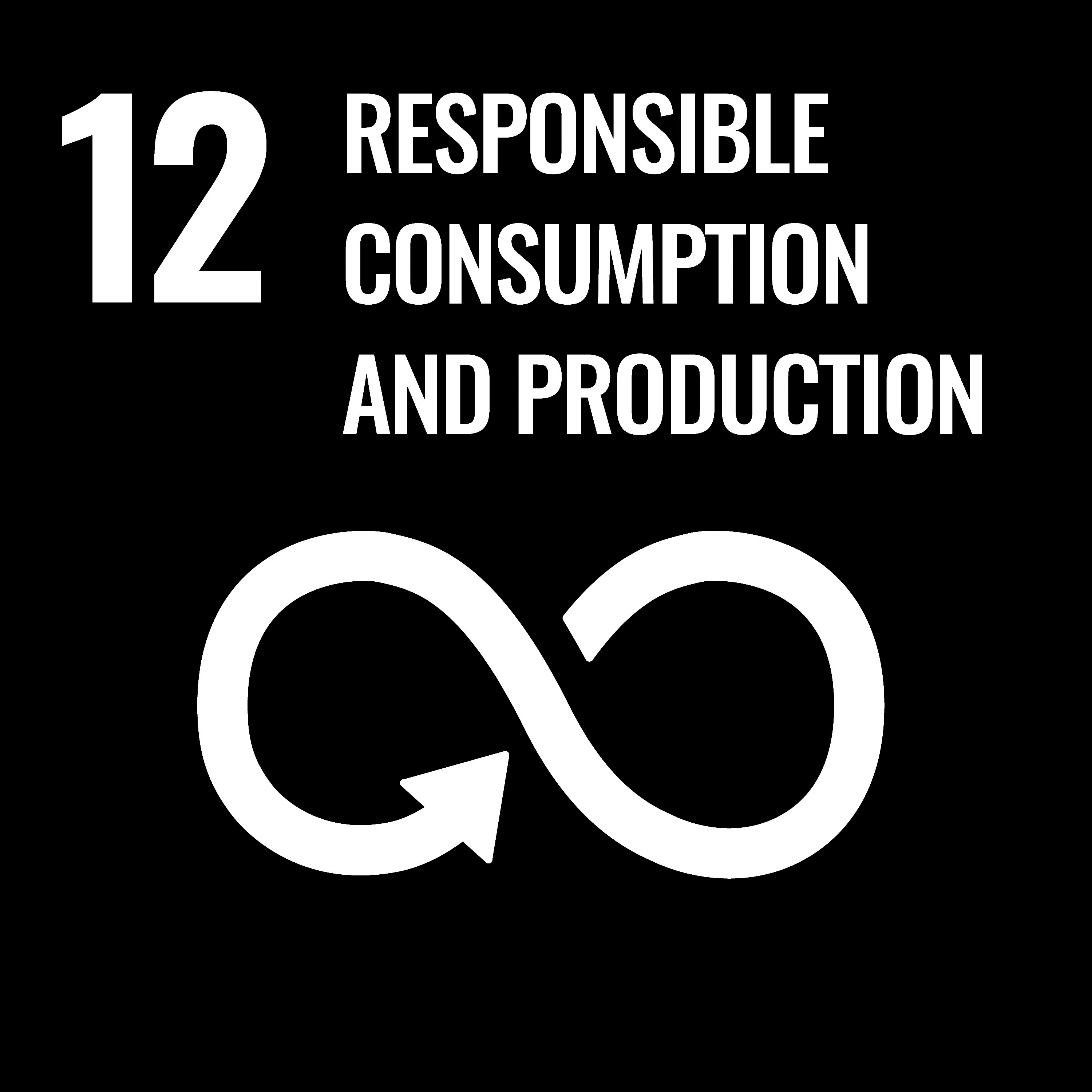
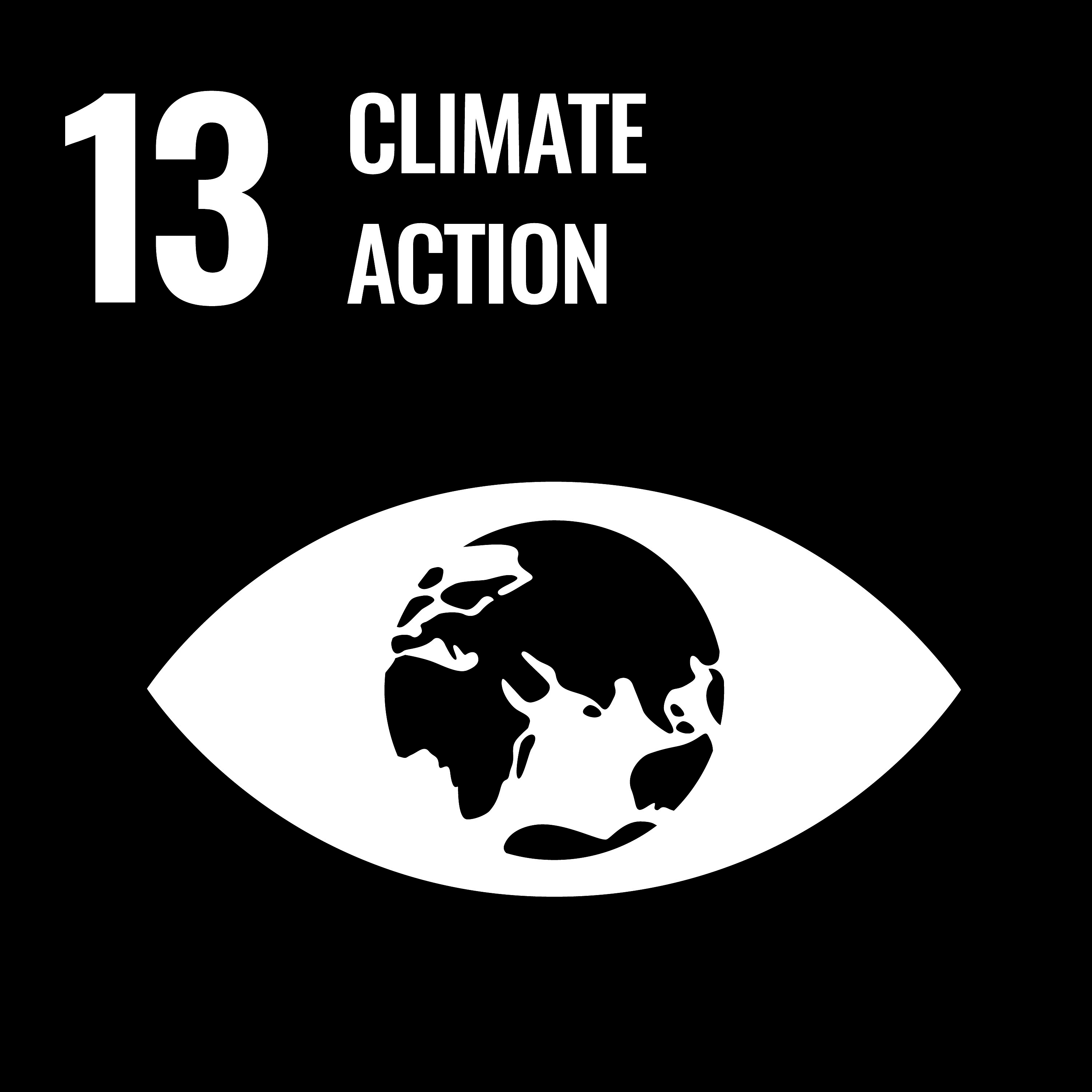
Our contribution to the SDGs
Licocare RBW Vita waxes contribute to SDG 12 and SDG 13. We’re enabling more sustainable material choices by increasing our own use of renewable and natural, non-food competing feedstock. We’re also facilitating manufacturers’ potential to reduce CO2 emissions by lowering their processing temperatures.
Our rice bran waxes are a great testament, a step closer to more sustainable plastics. Now these bio-based processing aids can even be used in polyester applications that require FDA approval, like infant care, food packaging, appliances, and water filtration, even more compounders and converters working with virgin and recycled engineering thermoplastics can use a low-carbon additive to improve efficiencies in their production processes.
Here’s how.
Turning challenge into benefit
Each year, 1.5 million tons of rice bran oil are produced globally, generating thousands of tons of crude rice bran wax as a by-product of processing raw rice into an edible oil. To help ensure maximum value is gained from a cultivated resource, we repurpose the valuable cereal grain’s “waste” into renewable-based high-performing lubricating and dispersing aids that promote more efficient, effective and sustainable plastics manufacturing.
These Licocare™ RBW Vita waxes are a positive contribution to a circular carbon economy, carrying our “Vita” designator because of their exceptionally high share of renewable carbon content – in this case 100%. Importantly, the multi-purpose additives hone in on key challenges facing carbon- and energy-intensive operations. In particular plastics processors’ needs and targets around efficiency improvements and carbon emission savings, while boosting product performance.
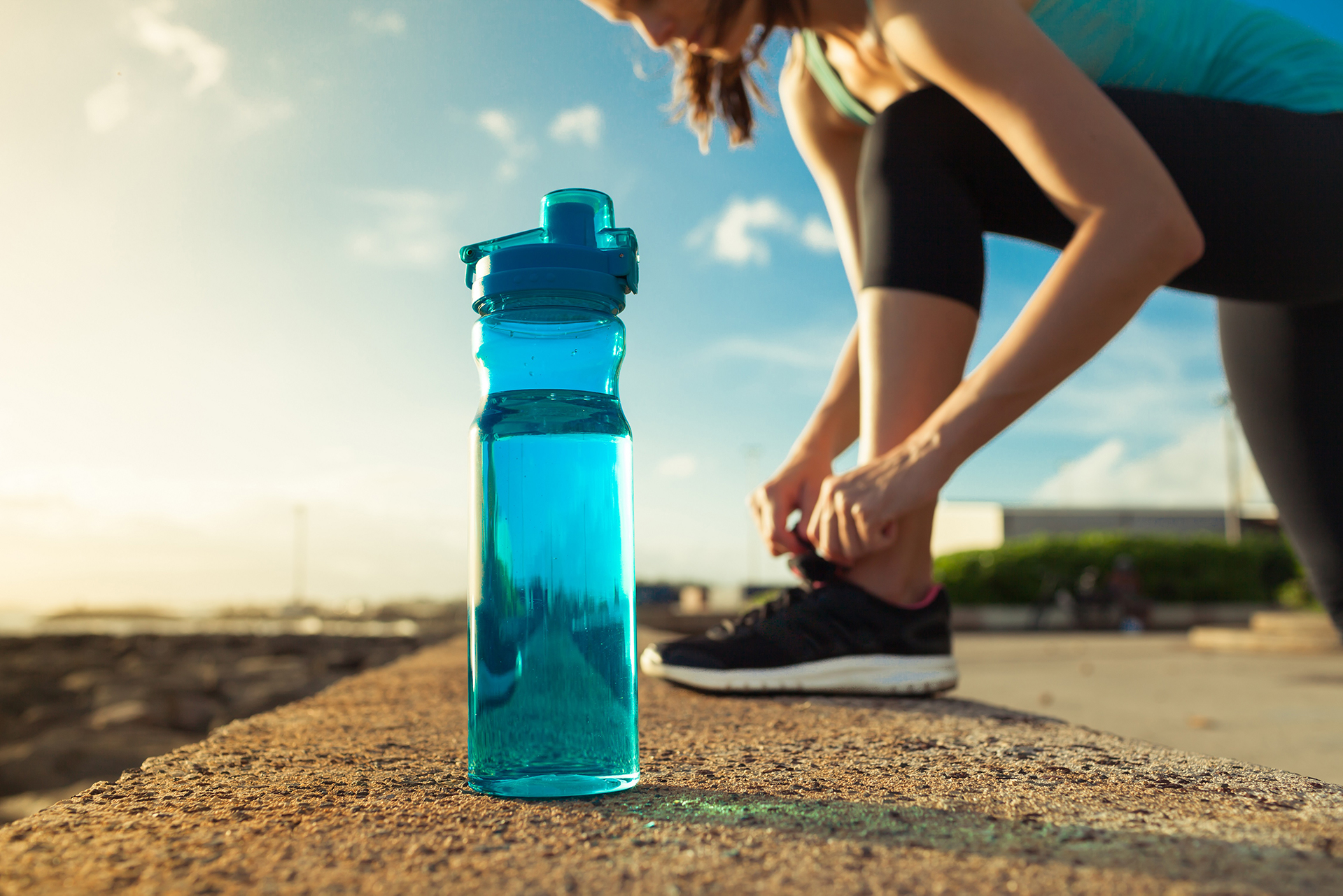
Licocare™ RBW Vita waxes make it easier to fulfill demanding end-application requirements for consistently smooth surfaces and filling difficult geometries
» It’s our mission for chemistry innovations to accelerate the transition from fossil carbon to renewable carbon, making change more viable at the manufacturing level. Ultimately these high-performing additives are about all in the supply chain contributing to the SDG goals of responsible consumption and production, and climate action, while staying competitive. «
Manuel Müller, Head of Strategy & Innovation Adsorbents & Additives
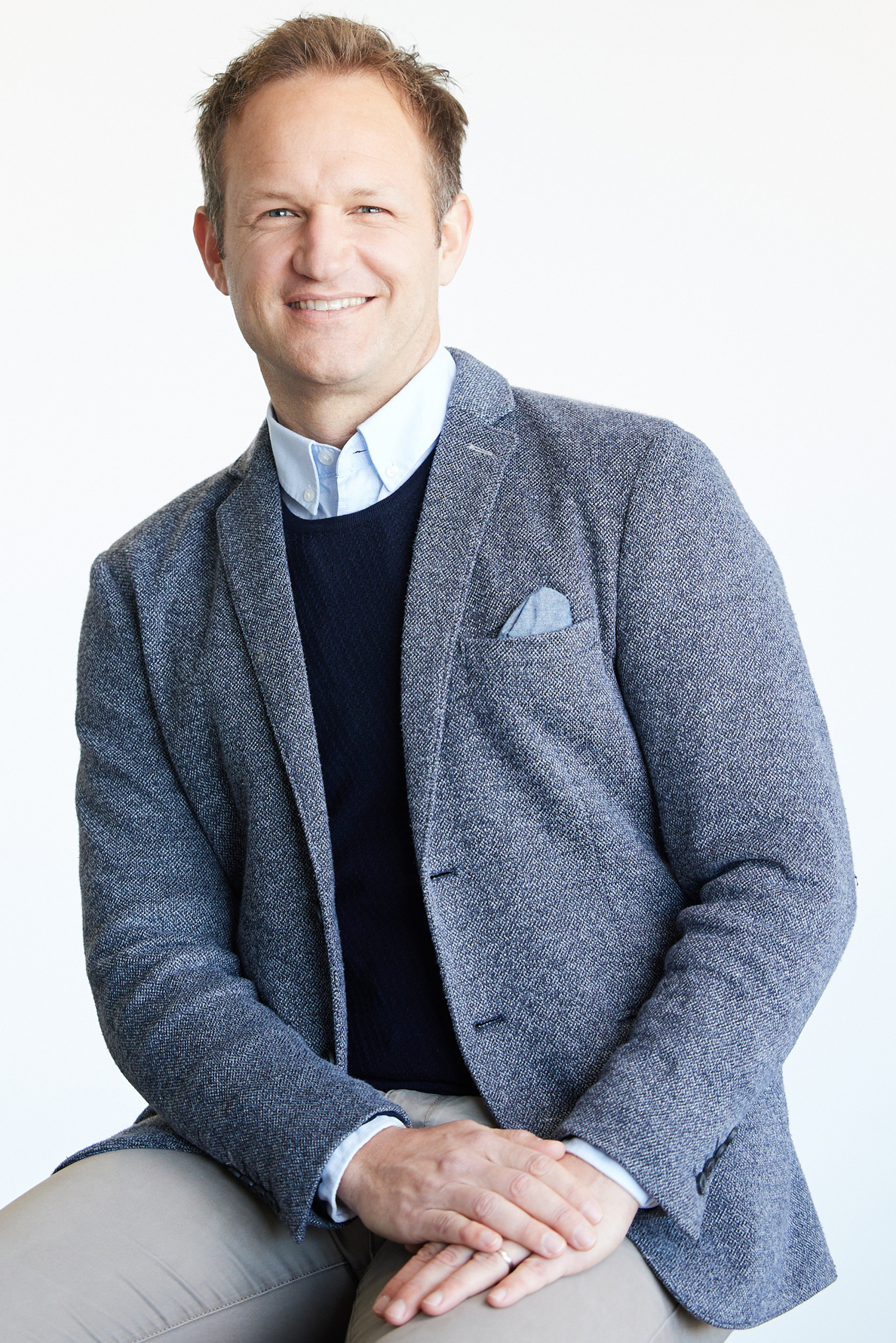
Carbon footprint reduction and enhanced performance
How do they help? In technical terms, Licocare RBW Vita waxes offer a low-carbon way to improve polymer melt flow and increase dispersion while reducing the force needed to remove injection molded parts or release film sheets.
On the factory floor, it becomes easier to fulfill demanding end-application requirements for consistently smooth surfaces and filling difficult geometries. Mechanical properties can also be enhanced, even when considering the increasingly relevant need to work with recycled content. Carbon generation and consumption can be reduced through faster processing at lower temperatures, leading to less energy use, fewer product rejections and less waste.
This is achievable because these renewable additives help polymers flow more quickly into molds and through dies with less drag and turbulence, enabling processing temperatures to be lowered and with that CO2 emissions too. Easier material release means much less time lost to stuck parts and cleaning. Even better, there’s less waste as any scrap can be reused, including in FDA-approved material, either for new packaging or for other applications like creating PET fibers for water filters or children’s clothing. And not forgetting the inventory advantage of having a set of ready-to-use additives approved for FDA and non-FDA applications.
All steps in the right direction for more sustainable plastics. Click here to find out more about how Licocare rice bran waxes are contributing to circular economy and greater manufacturing efficiency.
What makes this chemistry greater?
- Renewable feedstock – made from rice bran wax
- High performance – Fewer reject parts than attainable with available alternatives, better mold fill and reduced out-gassing (thus less gate blush due to high molecular weight of the RBWs), yields smoother surfaces, which results in better aesthetics and parts quality
- Smooth manufacturing – Better/faster melt flow and easier mold release than legacy solutions mean fewer process interruptions for sticking parts, resulting in more parts per hour
- Multi-functional – Selected grades provide combinations of benefits including lubrication, nucleation and improved pigment/filler dispersion to a wide variety of applications
- Faster molding cycles with reduced shrink and warp, gained from the nucleation and increased crystallinity promoted by Licocare RBW 330 Vita and RBW 560 Vita grades in polyamides and polyesters, respectively.