Working together to build the future of mining
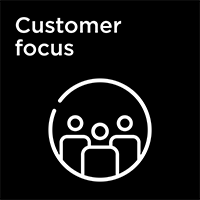
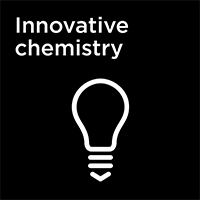
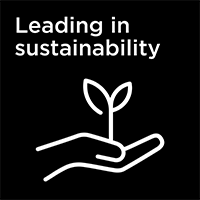
Delivering on Clariant's purpose »Greater chemistry - between people and planet.«
This story is an example of how Clariant delivers on its purpose-led strategy.
One of the most significant challenges that the mining industry is facing today is dealing with residual minerals, the so-called mining tailings. Simply put, tailings are all the minerals discarded in the beneficiation processes to produce metals and essential minerals.
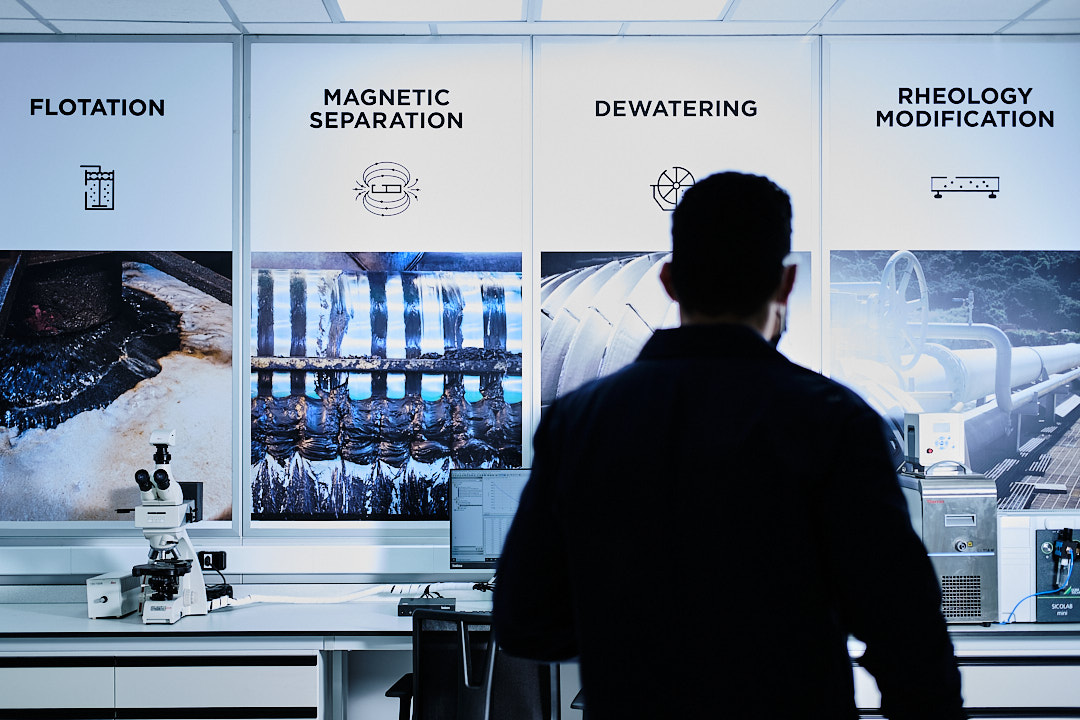
The mining of every metal and mineral produces tailings, with the largest contributors being copper mining (46%), gold mining (21%) and iron mining (9%). Mining companies are investing significant resources to comply with the highly regarded Global Industry Standard on Tailings Management or GISTM, which focuses on partnerships to implement and optimize the roadmap to prevent, reduce, recycle, recover, and store tailings in a sustainable and smart way.
Clariant Mining Solutions shares with its customers a sustainable vision for the future of mining to be a more efficient industry with fewer tailings. We are creating solutions for this challenge through our Tailings Management Program (TMP) and our global Competence Center for Tailings Treatment (CCTT) in Belo Horizonte, Brazil. In the cradle of Brazilian mining, the CCTT brings together state-of-the-art equipment and a highly qualified team to collaborate with our customers in developing specific solutions for their tailings needs, wherever they are in the world.
Working closely with our customers, our objective is to develop important and practical solutions that solve their biggest sustainability challenges, reinforcing our commitment to support the sustainability efforts of the global mining industry.
Today’s bottleneck
Tailings are the main by-product of extracting valuable materials from any mine. "Ground-up rock minus the gold," is how one gold miner puts it. Tailings are often moved and stored as a liquid slurry, and they can accumulate in large volumes. According to industry estimates, there are currently about 8,500 active and closed tailings storage facilities worldwide, holding some 217 cubic kilometers of tailings. Often tailings are stored in dams, which require ongoing monitoring.
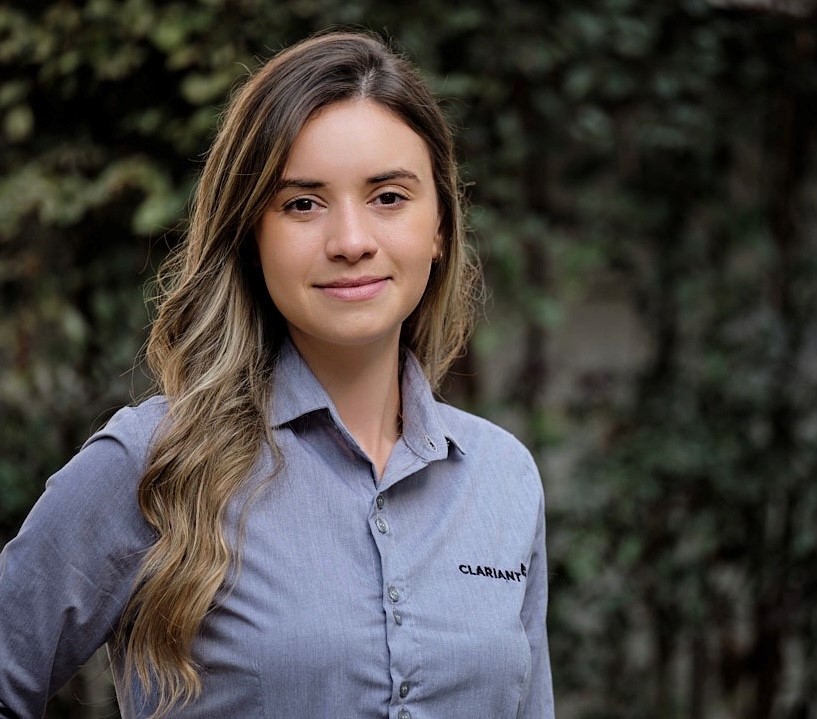
"Today, tailings management is the biggest safety challenge of the mining industry as well as the major bottleneck for most mineral processing plants; and at the same time mining is the key enabler for the sustainability megatrends, by supplying essential raw materials such as lithium, crucial for the production of renewable energy sources and electronic devices, including electric vehicles. We have the mission to deliver essential minerals in a more sustainable way, so we can support an eco-efficient value chain" says Livia Faustino. She heads Clariant's CCTT in Belo Horizonte after having dedicated years of academic and practical research – both in Brazil and in South Africa – to transform tailings into valuable resources.
At the CCTT, Livia and her colleagues use techniques such as flotation, magnetic separation, dewatering, and rheology modification to reduce the volume of tailings and tap into the value they still hold.
»Our passion is to develop tailor-made chemicals to reprocess tailings and extract valuable materials – transforming tailings from a cost into an asset for both the mining company and society: reducing the volume of tailings reduces the disposal costs and the footprint of mining operations, and the additional amounts of metals and minerals obtained become an additional source of revenue for the mining company.«
Livia Faustino, TMP Project Manager at Clariant
Draining the problem
"After conducting workshops with major mining companies, we now have more than 30 ongoing projects in partnership with key players worldwide," Livia says. For 2024, we will support the start-up and consolidation of several relevant tailings flotation projects to recover metals such as titanium, copper, lithium, phosphate, magnetite, and platinum.
Flotation is a powerful method for recovering valuable products both from primary and secondary mining. Magnetic separation and rheology modification also require specialty chemicals such that Livia and her team are delivering as innovative tools to optimize these processes in tailings treatment plants. The fourth key technical platform in Clariant’s program is specialty dewatering aids: "This allows us to significantly reduce tailings volumes as we maximize water recovery. We are also investing technology on filter aids for tailings filtration, which can double filter rates at the same time it reduces cake moisture content. This improves the plant’s productivity while also allowing dry stacking and can, in some cases, eliminate the need for tailing dams altogether," Livia explains.
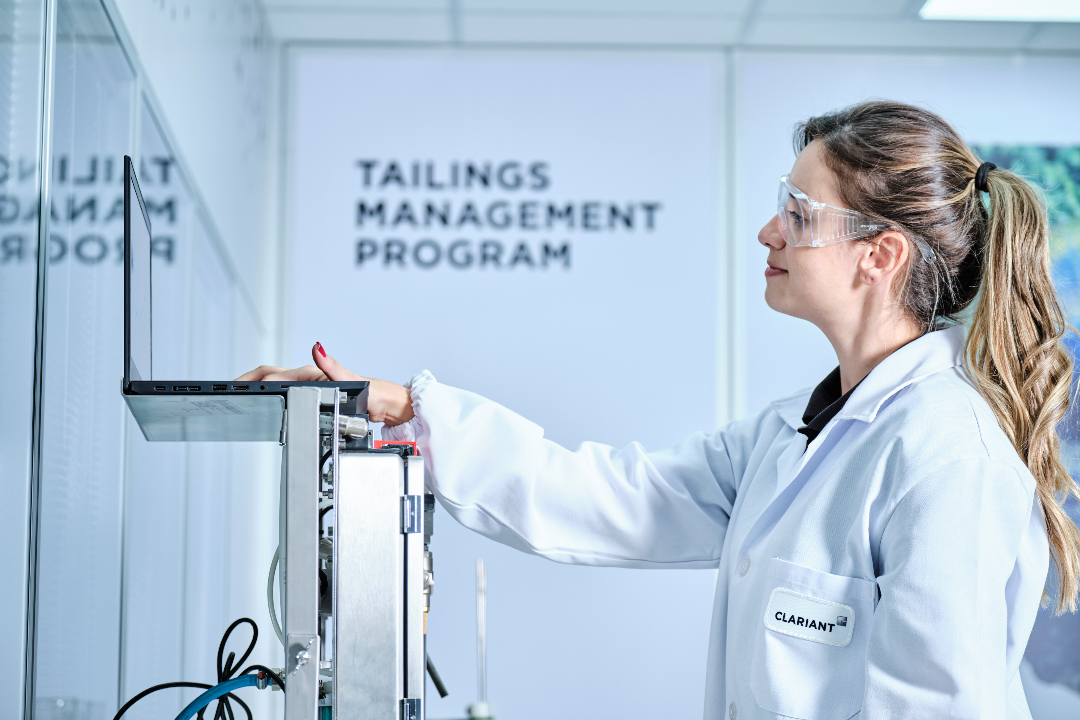
With today's tailing dams being some of the largest human-made structures on the planet, helping the mining industry improve its tailings management practices is how Clariant contributes to sustainable mining and its purpose “Greater chemistry – between people and planet.”
Clariant Mining Solutions has a strong legacy of providing chemical solutions co-created with our customers and partners that are more eco-friendly and more efficient. Our portfolio of specialty chemicals covers many applications – from flotation reagents and agglomeration additives to filter aids and emulsifiers for explosives.
Learn more here.