Fire protection – on steel and wood
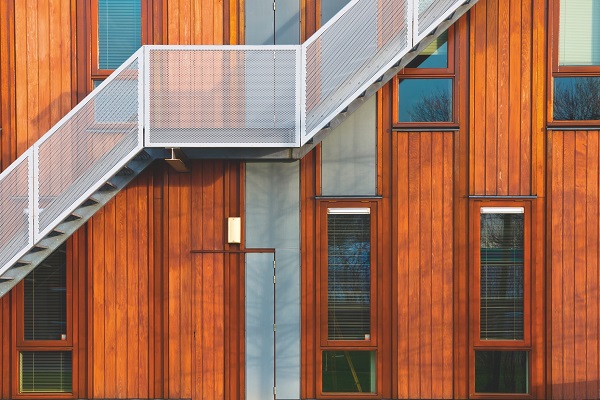
FIGURE 1
The protection of lives and assets in the case of fire is a crucial need in our modern life. As the proportion of houses higher than 20 meters has significantly increased over recent decades, the importance of fire protection, and especially structural fire protection, has also increased. Recent fire disasters, such as in Dubai or London, with the tragic Grenfell Tower fire with 79 fatalities, prove the significance of proper fire protection measures.
Intumescent coatings are widely used to protect steel structures from losing their structural strength during a fire for a certain amount of time, preventing the building from collapse and allowing people to safely evacuate. Intumescent foam can attain a thickness 10 to 100 times the originally applied coating, and insulates the substrate material through its low thermal conductivity (Figure 1). Exolit™ AP 422 and newly developed Exolit AP 435 (both ammonium polyphosphates) are key raw materials for the production of intumescent systems.Intumescent systems are ideal for combining attractive architectural appearance with fire safety, and aren’t just used on steel structures. Intumescent coatings can also be used on wood, which is highly sustainable and optically appealing, but is a combustible building material. As such, the special material properties of wood require the fire protection system to begin at low temperatures.
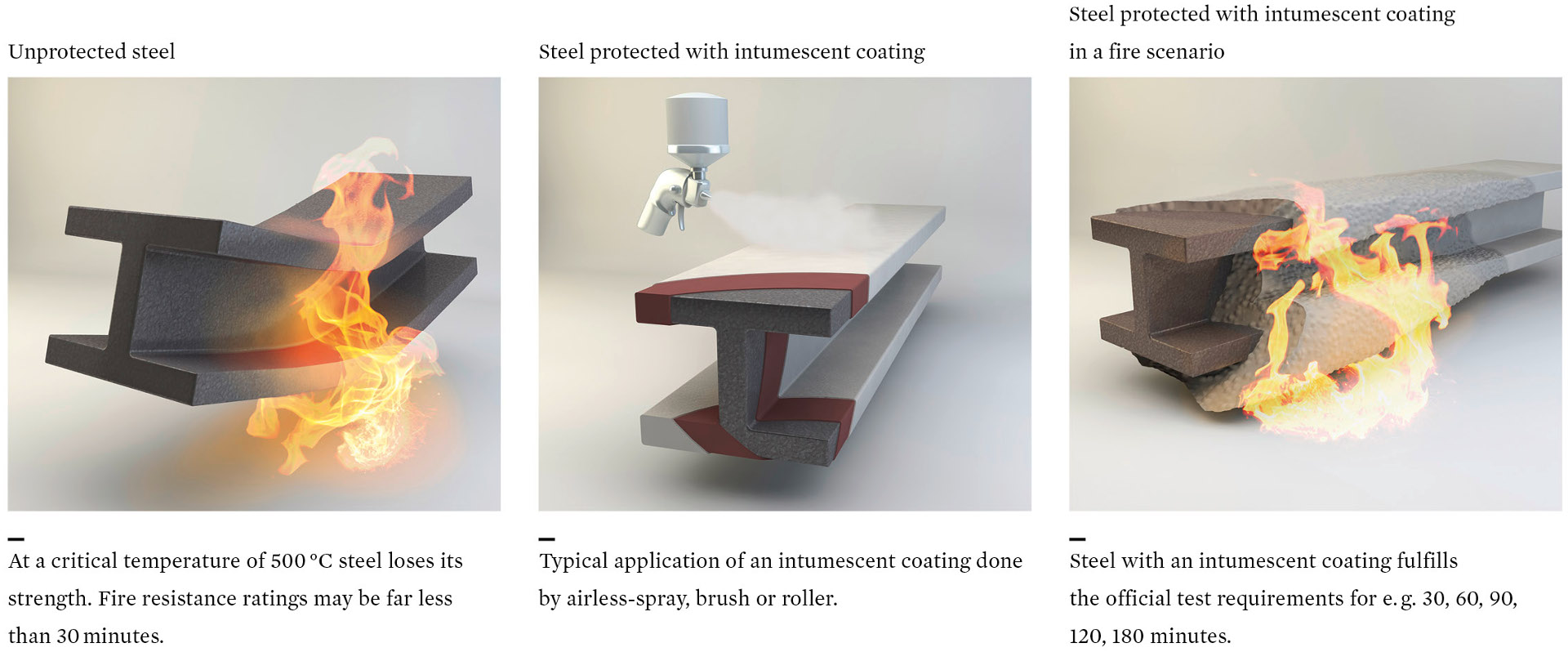
FIGURE 1
Viscosity-Stabilizing Flame Retardant That Keeps Intumescent Coatings Fluid and Workable
Waterborne intumescent coatings are increasingly popular because of their more environmentally friendly aspects compared to solvent-based coatings. Exolit AP 435 is a ground-breaking, halogen-free flame retardant that prolongs the shelf life of water-based intumescent coatings without affecting fire protection properties – therefore supporting the global trend towards VOC-free formulations.
Both producers and applicators of intumescent coatings require a low and stable viscosity of their waterbased formulations to achieve best coating results without additional rework or adjustments. The storage of water-based intumescent coatings may especially lead to an unacceptable increase in the viscosity level, limiting the shelf life of the compound and making the coating potentially inapplicable. Exolit AP 435 is not only characterized by a very low viscosity in aqueous suspension, even at elevated temperatures – its unique composition enables the intumescent coating to be stored at critical low temperatures (Figure 2).
Through its exceptional influence on the viscosity stabilization, it can fully replace Exolit AP 422 in waterborne and solvent-based intumescent coatings without affecting the fire protection properties. As can be seen in Figure 3, fire resistant times of 120 min can be easily achieved using Exolit AP 435 (dry film thickness, DFT = 2000 μm). In addition, there is no influence on the fire protection performance observed when Exolit AP 422 is replaced by Exolit AP 435.
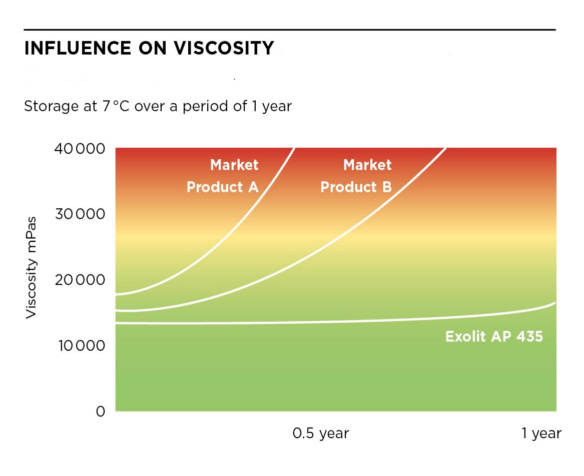
FIGURE 2
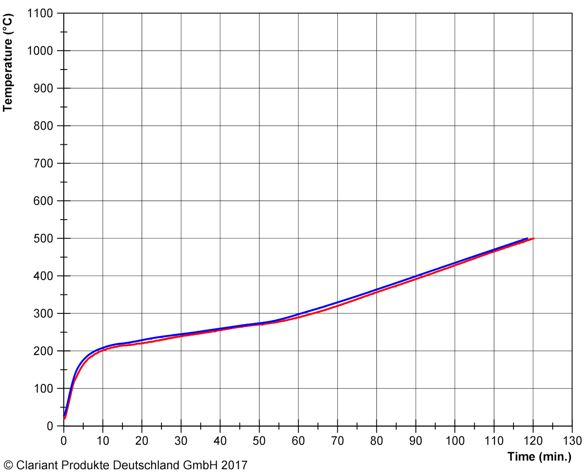
FIGURE 3
New Ingredient for Transparent Fire- and Water-Resistant Intumescent Wood Coatings
Wooden wall claddings and suspended ceilings are widely used in public buildings, but due to their ignitability and flame spread properties these materials cannot be used without appropriate fire protection. Pigmented FR coatings are widely known for this purpose, but they completely cover what is desired by architects, building owners and visitors – the beauty and natural appearance of wood.
Exolit 855 (TP) is a fire protection ingredient for transparent intumescent coatings on wood. It is a completely clear, almost colorless solution, enabling the combination of excellent fire and water resistance with light and dark wood surfaces (Figure 4). The product is a proprietary mixture based on liquid partial phosphoric acid esters. In combination with melamine formaldehyde resins it contains all the necessary reaction partners for an intumescent reaction, and reacts at lower temperatures than conventional systems. Therefore, the intumescent system can be applied on almost all wooden surfaces, e.g., solid wood, medium-density fiberboard, chipboards, plywood and veneered wood.
The intumescent system consists of a two-component formulation. Part 1 is represented by the melamineformaldehyde resin, several additives and the solvent (water). Part 2 contains Exolit 855 (TP), a hardener and further components. The pot life of the combined parts is about 3 hrs and can be easily applied using brush or airless spray gun. The guide formulation (offered by Clariant under a nondisclosure agreement) shows good flow and levelling properties. The coating cures at ambient temperature, is dryto- touch after 4 hrs and scratch resistant after 24 hrs. An additional topcoat may be beneficial for protection against high humidity and direct water contact.
The intumescent system consists of a two-component formulation. Part 1 is represented by the melamineformaldehyde resin, several additives and the solvent (water). Part 2 contains Exolit 855 (TP), a hardener and further components. The pot life of the combined parts is about 3 hrs and can be easily applied using brush or airless spray gun. The guide formulation (offered by Clariant under a nondisclosure agreement) shows good flow and levelling properties. The coating cures at ambient temperature, is dryto- touch after 4 hrs and scratch resistant after 24 hrs. An additional topcoat may be beneficial for protection against high humidity and direct water contact.
When tested in a cone calorimeter test (iCone; 50 kW; distance 25 mm) on a pine wood substrate (400 g/m² wet) the intumescent coating shows outstanding fire protection performance, as shown in Figure 5. While the total Total-Heat-Release within 600 sec testtime (THR 600) is reduced by 98%, the maximum average rate of heat emission value is reduced by 67% compared to the noncoated panel.
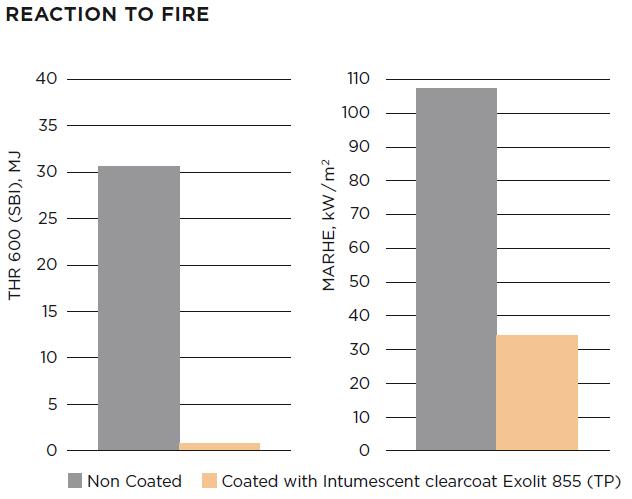
FIGURE 5
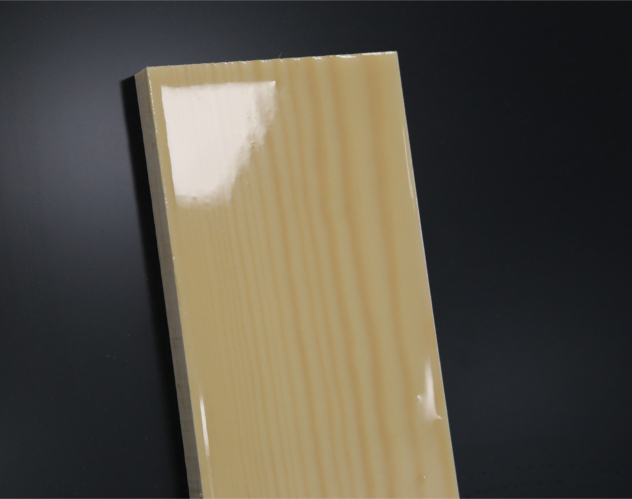
FIGURE 4
When tested in a cone calorimeter test (iCone; 50 kW; distance 25 mm) on a pine wood substrate (400 g/m² wet) the intumescent coating shows outstanding fire protection performance, as shown in Figure 5. While the total Total-Heat-Release within 600 sec testtime (THR 600) is reduced by 98%, the maximum average rate of heat emission value is reduced by 67% compared to the noncoated panel.
Conclusion
When trying to ensure the fire safety of steel structures in public buildings and other spaces, architects used to have to rely on solutions that could easily detract from the aesthetic beauty of their work. As components of perfectly safe but still highly attractive intumescent coatings, both Exolit 855 (TP) and Exolit AP 435 support the usage of innovative and attractive protection techniques. The safe use of a sustainable, ecological - yet flammable - construction material while retaining its elegance and beauty paves the way for one perfect combination - classic design and the highest safety standards.
Author: Dr. Klaus Bender, Technical Service Coatings & Dr. Andreas Termath, Prodcut Expert Exolit AP, Clariant Plastics & Coatings (Deutschland) GmbH, Huerth, Germany
Published by: Paint & Coatings Industry (PCI)