Fueling our cars with straw
Using a non-food energy source to reduce CO2 emissions
In light of growing climate change concerns, many countries have set targets to continuously reduce greenhouse gas emissions with a focus on the transport sector. Why? A large part of CO2 emissions are produced in the mobility sector. In fact, almost a quarter of Europe’s and the United States’ respective greenhouse gas emissions stems from transport.
How can we sustain our increasingly mobile lifestyles while reducing the impact on our planet?
Enter biofuels -- fuels produced using renewable energy sources such as corn, soy, or agricultural by-products that are naturally replenished and renewable as opposed to fossil fuels such as coal or crude oil. The latter are considered to be non-renewable since they are derived from deposits the earth has built up over millions of years.
"Industry, and society as a whole, face the challenge of maintaining economic growth and quality of life in a sustainable way."
What’s more, whereas fossil fuels usually require transport across the globe, renewable fuels can typically be grown close to where the energy demand is.
Biofuel types
Not all biofuels are the same though -- they differ in feedstock sources and conversion technologies, with a distinction commonly made between first and second-generation biofuels. First-generation biofuels are made from the plant’s crop which contains sugar, starch, or oils that can relatively easily be converted into fuels. Second-generation or advanced biofuels, on the other hand, are harder to produce. They are derived from non-food renewable sources such as agricultural or wood residues, or other waste materials that have a more stable structure and thus are more difficult to break apart to access the sugars.
One example of an advanced biofuel is cellulosic ethanol produced from agricultural residues like straw. It provides exceptionally high greenhouse gas savings and can be used in our existing car and energy infrastructure. This makes cellulosic ethanol an indispensable resource in decarbonizing the transport sector and in reaching global climate protection goals.
Moreover, by using agricultural residues such as straw, cellulosic ethanol can extend current biofuel production to new, currently underutilized non-food feedstock and improve the overall performance of biofuels.
The sunliquid™ process
To address the need for an efficient and economical production of advanced biofuels such as cellulosic ethanol, Clariant has developed a process called sunliquid which converts plant residues that would otherwise be discarded, such as cereal straw, corn stover or bagasse, almost entirely into high-value bioethanol.
The sunliquid technology offers a comprehensive, entirely integrated process design with innovative technology features that can be tailored to specific local needs and conditions.
The technology also provides a tangible example of a circular economy; various types of locally sourced raw materials can be substituted in the process, for example corn stover in North America, sugar cane bagasse in South America, rice straw in Asia, or wheat straw in Europe, and the by-products from the sunliquid process (lignin and vinasse) can be re-used locally for energy production and as an organic fertilizer.
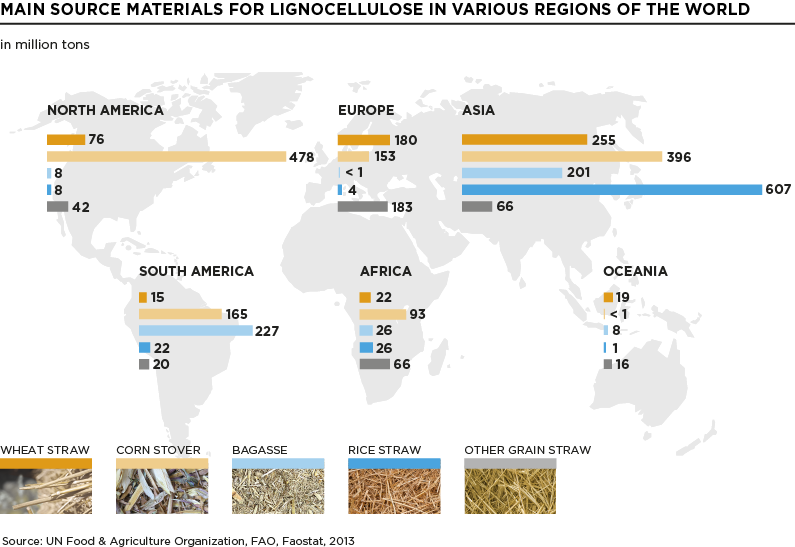
Bioethanol produced with the sunliquid process saves around 95 percent of greenhouse gas emissions compared to gasoline, and the process itself is self-powered since it uses the by-product lignin to produce the necessary energy (electricity and steam) required to run the process. The enzymes needed to extract the sugars from the straw are produced within the process, making it much more affordable. In addition to being energy self-sufficient and more cost efficient, the process also results in 50 percent more ethanol production than other processes.
To demonstrate sunliquid’s potential, Clariant built Germany’s first and largest pre-commercial cellulosic ethanol plant in 2012. Located in Bavaria, the plant produces up to 1,000 tons of bioethanol annually.
Test with Mercedes-Benz and Haltermann Carless
To prove the bioethanol’s performance, Clariant, together with Mercedes-Benz and Haltermann Carless, conducted a fleet test with Mercedes-Benz vehicles. In the field, the fuel mix with a 20 percent make up of cellulosic ethanol produced at Clariant’s sunliquid™ plant proved to be just as performant as today’s standard fuels. The E20 fuel also had much lower particle count emissions compared to the EU reference fuel Euro 5, and contributed to overall engine efficiency with potential to help reduce future engines’ fuel consumption.
“Industry, and society as a whole, face the challenge of maintaining economic growth and quality of life in a sustainable way,” says Markus Rarbach, Head of Business Line Biofuels and Derivatives at Clariant. “While fossil resources make up a huge part of feedstock in the chemical industry currently and in the foreseeable future, it is important for chemical companies to investigate alternative resources that support high-quality products. Sustainable processes that use renewable raw materials will be key to moving forward, and Clariant embraces these innovations,” he says.
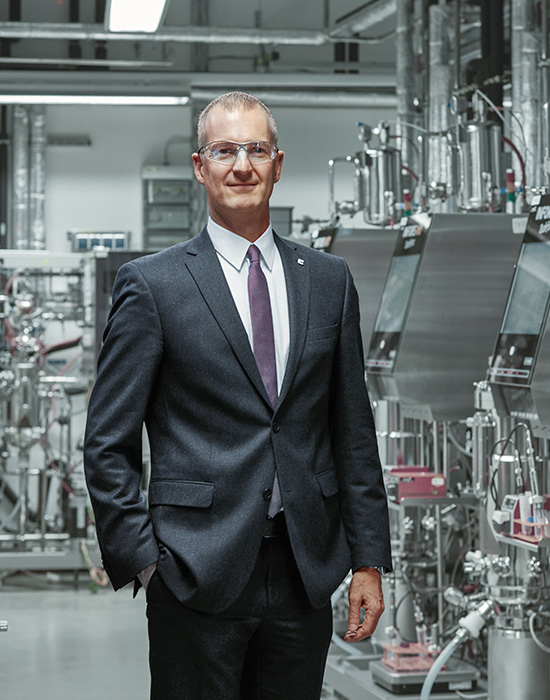
The spotlight on advanced biofuels is more intense than ever. The EU Parliament recently voted for a 12% renewables target for the transport sector by 2030, 10% of which should come from advanced biofuels and low carbon fuels -- and there are similar discussions occurring in other areas around the world.