From concept to reality: How Clariant Custom Catalyst Manufacturing delivers on innovation and customer centricity
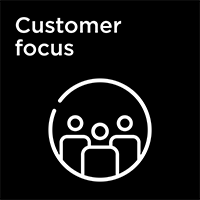
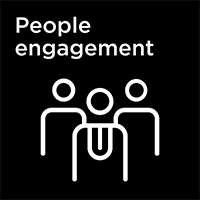
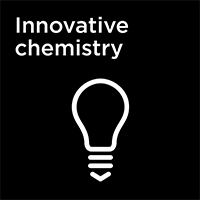
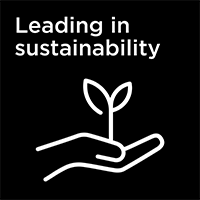
Delivering on Clariant's purpose »Greater chemistry - between people and planet.«
This story is an example of how Clariant delivers on its purpose-led strategy.
In the following interview, Nora Schiefenhoevel, Head of Business Development & Custom, talks about how Clariant’s Custom Catalysts Manufacturing supports customer focus – one of Clariant’s purpose dimensions, and how we are shaping the future together with our customers through collaboration and innovation.
Who and why would someone need a custom catalyst solution?
Our customers use catalysts in manufacturing to facilitate a chemical reaction. It could be for a broad range of applications – say, in a petrochemical plant or in a refinery, or even for an emerging technology like plastic recycling, CO2 utilization, hydrogen transport, or Sustainable Aviation Fuel.Since each customer has a different need and each application requires different performance criteria, off-the-shelf catalysts just don’t always provide the best performing, most efficient or sustainable results customers are looking for.
Many times, our customers have already developed a catalyst or adsorbent recipe in their own lab. However, the chance of success increases tremendously when customers engage with us. We are experts in the field and have the proper equipment to scale-up and produce these lab-made catalysts. This ensures that the commercial catalyst will perform very similarly to the lab catalyst in the commercial operation of the customer, and that it can be produced in a safe, sustainable, and cost-efficient way.
And that’s why customers turn to Clariant: Our expertise and collaborative feedback help save overall cost and increase speed to market. We help optimize the catalyst, develop a manufacturing process, scale it up, and then produce to our customer’s specification thanks to our strong R&D and manufacturing know-how. What we’re doing is taking our customer’s concept and helping them turn it into reality.
Is tolling the same thing as custom manufacturing?
There’s a difference, actually. Custom manufacturing starts much earlier. It works well for companies that have R&D but cannot produce catalysts commercially. As mentioned in the previous example, we use the customer’s lab recipe, scale it up, develop a production process and produce within the spec. Tolling with Clariant is possible, too. Here a commercial recipe is already defined, we adapt it to our assets, and then produce the catalyst. The raw materials are typically provided by the customerBut our sweet spot is custom manufacturing. Why? Successfully manufacturing catalysts from start to finish is very difficult, and many other companies only offer tolling of a single step of the production chain. At Clariant, we are specialized in scaling up all required steps to make a catalyst – those steps are often interlinked with each other and Clariant optimizes the whole process to ensure that the catalyst is fine-tuned to the customer’s needs.
In addition to tolling and custom catalyst manufacturing we can also provide third party R&D services to develop a new catalyst, to optimize a catalyst lab formulation, or to develop shaping a recipe. Depending on the situation, joint developments are also possible. So we are quite flexible.
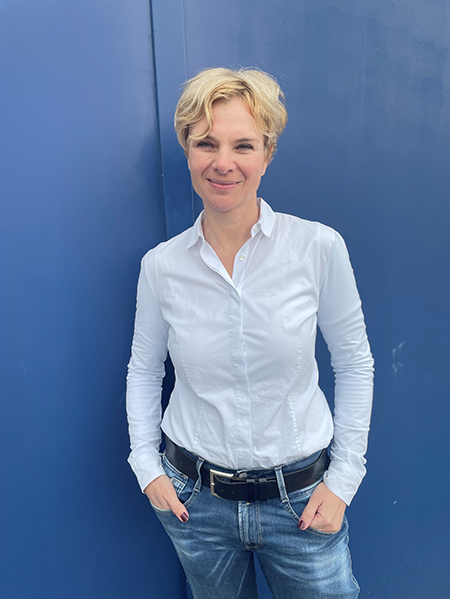
»What we’re doing is taking our customer’s concept and helping them turn it into reality.«
Nora Schiefenhoevel, Head of Business Development & Custom at Clariant
Tell me more about Clariant’s experience and strengths in custom catalyst manufacturing.
We have over 70 years in catalyst expertise and innovation with global R&D, scale-up, and manufacturing capabilities. Our team has specialized expertise across an incredibly wide range of materials and structures and preparation technologies. This allows us to take on many different types of highly complex custom projects.Our R&D stands out because we’ve stayed on the cutting edge by continuing to invest heavily in innovation, our global R&D capabilities, as well as state-of-the-art manufacturing technologies. For example, one of our specialties is leveraging high-throughput experimentation. This allows us to screen thousands of options in parallel, rapidly discovering the optimal formulations in just weeks or months instead of years.
We have 10 R&D centers globally, and we launch over 20 new catalysts per year on average. Clariant’s capabilities and equipment meet our customer’s needs with dedicated assets for customers and multipurpose lines, multiple manufacturing lines for production trials, identical unit operations in pilot and commercial scale for faster scale-up, and a dedicated custom team to ensure firewall and IP protection.
We offer numerous different catalyst production capabilities, such as precipitation, impregnation, calcination, tableting, spray drying, coating, and much more. In addition, the R&D services run the gamut from material characterization, improvements in physical properties, and studies of effects of contaminants on activity and stability.
Do you have any examples? Why do customers choose Clariant for custom catalysts?
R&D, catalyst know-how, and capabilities are one thing, but it’s more than that: We develop strong relationships with our customers and collaborate closely with them to develop solutions.At the end of the day, we are saving our customers time and cost. Here’s a real-life example: We recently announced that we’re collaborating with Air Company, located in New York, that developed a technology to transform CO2 into sustainable jet fuel. After developing a first catalyst lab recipe, Air Company partnered with Clariant to scale-up its catalyst recipe. Clariant is working to further optimize and transfer the recipe to full-scale production.
We’ve already seen the success in our collaborative development: During the process, Clariant has been able to help reduce processing time by 8x with our proposed drying method; this translates to reduced energy consumption and lower cost. Product throughput increased by 4.6x, which will translate to lower water consumption per kilogram of product as well as time savings. The overall cost is significantly reduced with our expertise, and pilot scale-up is anticipated for the end of 2024 with commercialization targeted in 2025.
We were recently honored to receive the following feedback from Stafford Sheehan, Co-Founder & Chief Technology Officer at Air Company: »Clariant's expertise in catalyst scale-up is the best in the industry, which makes our collaboration a perfect match given our focus on catalyst discovery and reactor engineering. We're honored to work with the custom catalyst team and proud to be partners as we scale up our carbon dioxide utilization technology.« We are looking forward to the next steps on this exciting project!
Learn more about Custom Catalysts Manufacturing here.