sunliquid™
Converting straw to advanced biofuels with sunliquid™
Cellulosic ethanol from agricultural residues – Sustainable mobility with sunliquid™
A shortage of fossil resources, energy security, climate change, environmental protection – these are the issues concerning us today in the energy sector. Alternative sources of energy must be found to reduce our dependence on oil and nowhere is this more evident than in the transport sector. In the European Union, the US and other major economic areas, politicians have laid down basic frameworks to promote the use of climate-friendly biofuels.
Many companies show a growing interest in the production of ethanol from renewable lignocellulosic resources, such as agricultural residues. These resources are created in sufficient quantities worldwide as a by-product of current agricultural practices, as in the case of straw from cereal production.
The sunliquid™ process developed by Clariant meets all the requirements of a technically efficient, innovative process for converting agricultural residues into climate-friendly biofuel. Using process-integrated enzyme production, optimized enzymes, simultaneous conversion of cellulose and hemicellulose into ethanol and an energy-efficient process design, it has been possible to overcome major technological challenges and reduce production costs.
Cellulosic ethanol from agricultural residues - Think ahead, think sunliquid
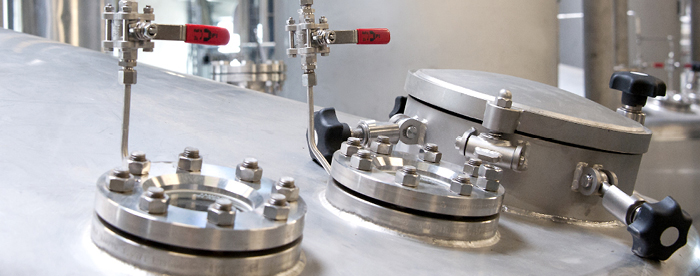
We offer comprehensive cellulosic ethanol solutions with integrated and therefore autonomous enzyme production. Our aim was to develop a process offering high yields at minimal cost. To this end, we have combined our patented processes with state-of-the-art technology to set ourselves apart from other companies.
Various types of feedstock are converted into cellulosic ethanol after undergoing pre-treatment, enzymatic hydrolysis and fermentation. Our integrated enzyme production gives rise to the lowest possible process costs.
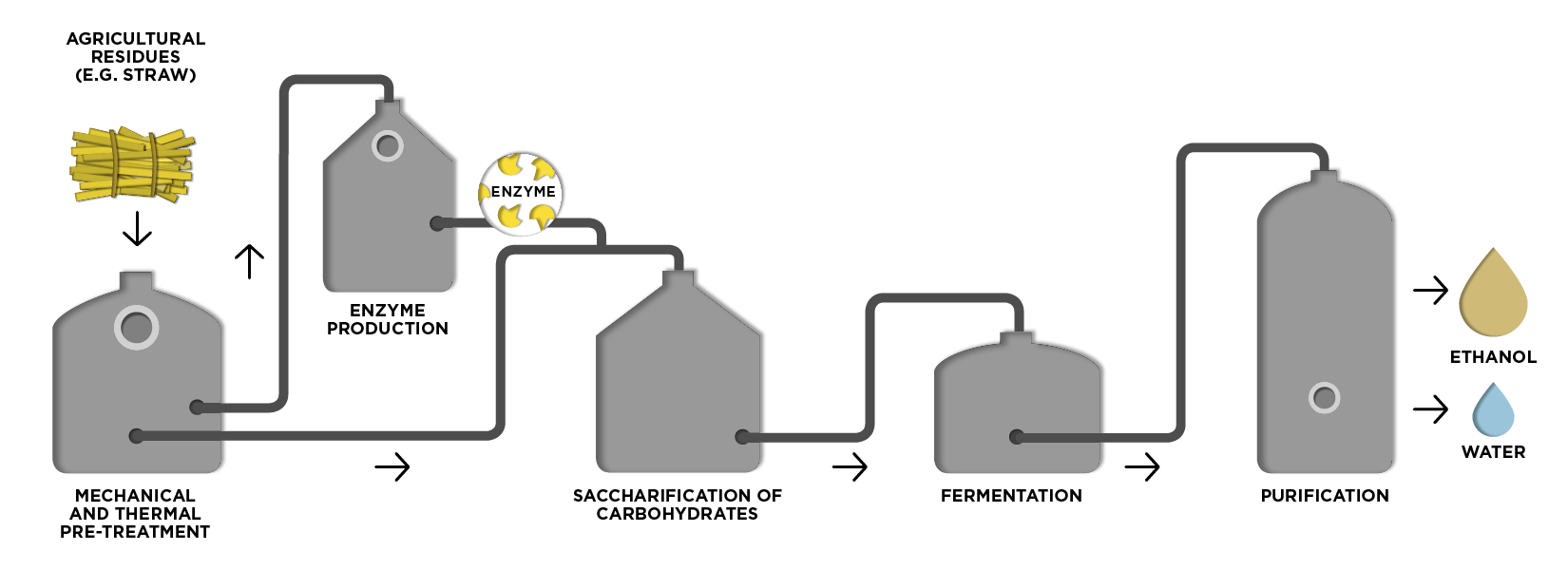
The sunliquid™ process
Pre-treatment
Chemical-free pre-treatment lowers production and investment costs. At the same time, environmental, health and safety risks are minimized.Enzyme production
A small percentage of the pre-treated feedstock is used for enzyme production, which is an integrated part of the process and takes place on-site at the ethanol plant. This makes a major contribution to the economic efficiency of the overall process, resulting in a significant reduction in production costs and ensuring independence from supply shortages and price volatility.Enzymatic hydrolysis
A bespoke enzyme mixture hydrolyses cellulose and hemicellulose chains to form sugar monomers. This step is also termed saccharification. The enzymes are highly optimized based on feedstock and process parameters, resulting in maximum yields and short reaction times under optimal conditions.Fermentation
Using optimized microorganisms, the sunliquid™ process provides for efficient fermentation, giving rise to maximum ethanol yields. This highly-optimized, one-pot system simultaneously converts both C5 and C6 sugars to ethanol, delivering up to 50% more ethanol than conventional processes which convert only C6 sugars.Product purification
The innovative and highly energy saving purification method reduces energy demand by up to 50% compared with conventional distillation. It is based on thorough process planning and energy integration.
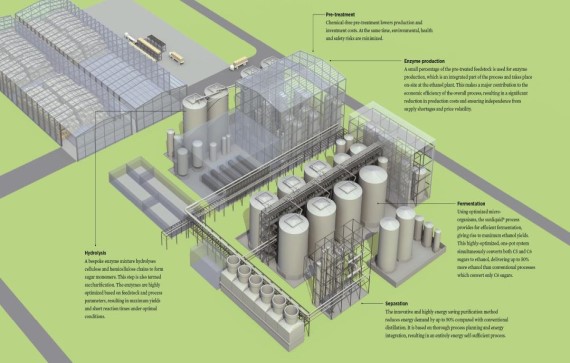
Cellulosic ethanol from agricultural residues - Think ahead, think sunliquid
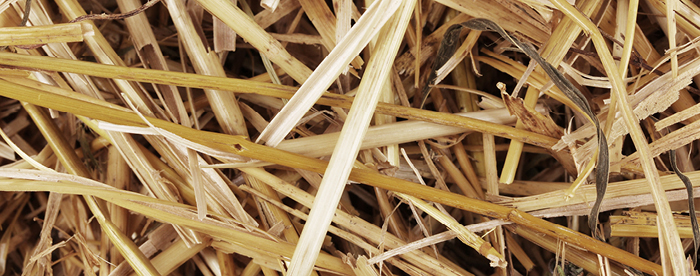
Feedstock of the future – lignocellulosic agricultural residues
Lignocellulose is the feedstock used for our sunliquid™ process. Lignocellulose provides structural support for cell walls in biomass gained from forestry and farming. Its stable structure is made up of cellulose, hemicellulose and lignin, the exact composition varying according to the type of plant. Within a short time, we were able to adjust our sunliquid™ process to the most varied types of feedstock, including cereal straw, corn stover, bagasse, or energy crops such as miscanthus and switchgrass. We have processed wheat-straw, corn stover and bagasse at our demonstration plant in Straubing showing good results. A number of other lignocellulosic feedstock have been tested at pilot and lab scale.
Availability of lignocellulosic feedstock
The USA, Asia, and the European Union are the leading producers of agricultural products. At a regional level, various straw sources are available for extracting lignocellulose-based ethanol: While the focus in Europe is on the residues of wheat and barley production, in Asia large quantities of rice straw are available (while millet straw is dominant amongst the other types of cereal straw), in North America it is corn stover and in South America bagasse as a by-product of sugarcane production.
A study by the International Council on Clean Transportation (ICCT) estimates the realistic amount of agricultural by-products like straw that will be available in Europe in 2030 at 139 million tons – compared to 122 million tons in 2013.
About 380 million tons of straw from wheat and other cereal and about 150 million tons of corn stover are produced every year in the EU alone. Studies expect this quantity to increase in coming years due to the growth in grain farming. Only a small fraction is currently returned to the field, used for livestock farming, or for mushroom cultivation. A study comparison shows that, depending on the region and the local conditions, up to between 30 and maximally 60 percent of the straw produced can be removed from the field and made available for further use.
The Brazilian Energy Plan scenario estimates that almost 26 million tons of bagasse will be available in 2030. Due to the high price fluctuations, combined processes in which refineries produce bioethanol as well as electricity are considered economically viable.
In the USA, corn stover is the main raw material, while part of this is also required to fertilize the soil. A study by the U.S. Department of Energy shows that the supply of raw materials is likely to undergo a fundamental change in the next twenty years. Besides agricultural waste products, the authors are forecasting an increase in energy crops, such as various species of grass and algae.
By 2040, almost 600 million additional tons of plant residues and special energy crops could be available for the generation of renewable energy sources in the USA.