Exceptional catalysts for efficient
blue hydrogen production
Large-scale production of low-carbon hydrogen (known as blue hydrogen) is an important step towards reducing global carbon dioxide emissions. The technology is comparable with today’s grey hydrogen production from fossil fuels but includes additional carbon capturing and sequestration (CCS) to permanently remove CO2 for storage or further use.
Clariant has been developing leading catalysts for hydrogen production technologies for many decades. Through our innovative catalytic solutions and strong process partners, we can optimize the efficiency of blue hydrogen production and support the expansion of this low-carbon technology.

HIGHEST ENERGY
EFFICIENCY

CO2REDUCTION

LOWEST
POSSIBLE COSTS
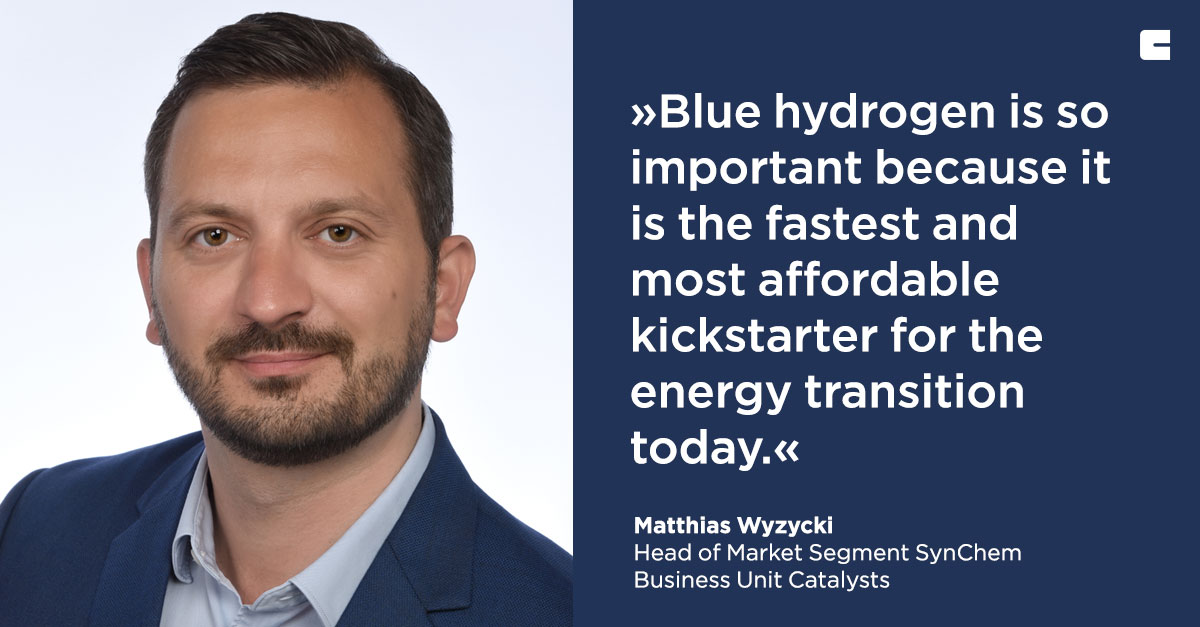
PODCAST
Blue hydrogen: Production pathways,
technologies and its importance in the
global energy transition
Hydrocarbon Processing
Three paths to low-carbon hydrogen
The technologies currently available for blue hydrogen production include steam methane reforming (SMR hydrogen); autothermal reforming (ATR hydrogen); and partial oxidation (POX hydrogen). They differ in their catalyst requirements, and their potential to reduce CO2 emissions for sequestration. Clariant offers high-performance catalysts for cost-efficient blue hydrogen production via all these methods.
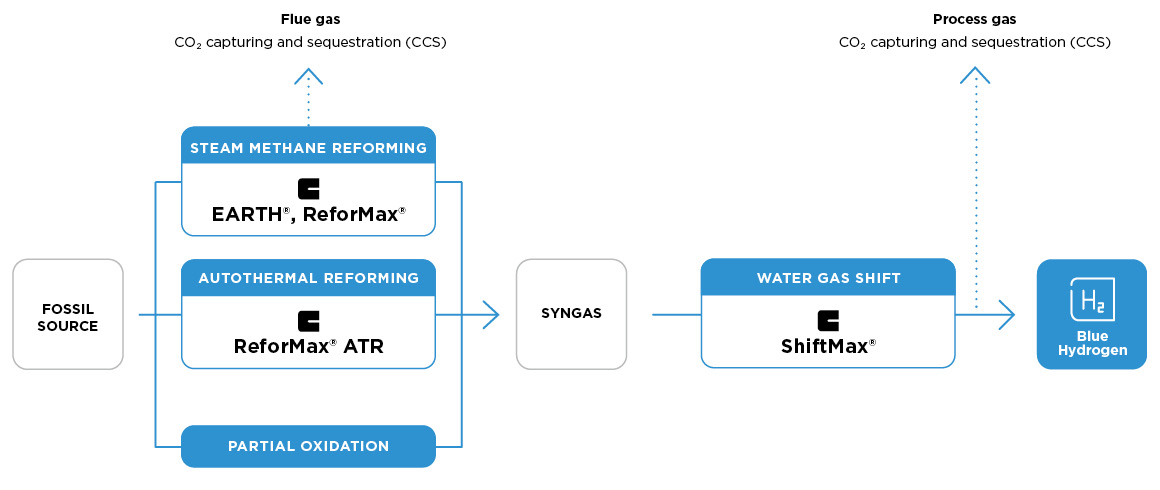
Blue hydrogen via steam methane reforming
Steam reforming is a principal industrial process used to manufacture synthesis gas (syngas) for the production of hydrogen, ammonia and methanol. The heart of the process is the tubular primary reformer in which hydrocarbon feed (e.g., methane) reacts catalytically with steam to form a mixture of H2, CO and CO2. Despite its many advantages, the steam reformer is a major carbon dioxide emitter. Now, innovative Clariant catalysts are used in Technip Energies’ ground-breaking EARTH™ technology to drastically improve the energy efficiency of SMR based hydrogen production, thus significantly reducing CO2 in the flue gas.
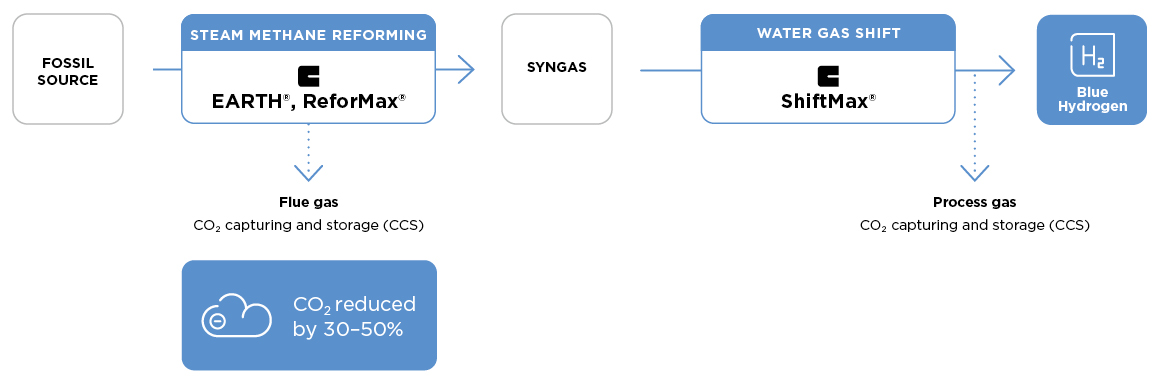
EARTH technology & catalysts
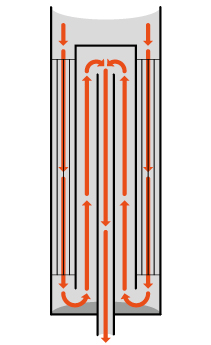
Developed and patented by Technip Energies, EARTH (Enhanced Annular Reforming Tube for Hydrogen) technology comprises a concentric tubular assembly in the steam methane reformer with a structured catalyst loaded in the outer annular space. The unique setup ensures simultaneously superior heat recuperation and higher throughput in steam reforming process.
© TechnipFMC - Concentric tubular structure of EARTH technology showing internal flow recirculation
The novel catalyst, developed by Clariant and Technip Energies, combines low pressure drop with highest activity and heat transfer. Not least because of its outstanding stability and mechanical robustness, the catalyst delivers excellent performance despite the thermal and mechanical stress of the reforming process, and the reduced volume of the EARTH catalyst bed.
Compared to the performance of traditional catalysts in a standard reformer, EARTH allows to increase the hydrogen yield by up to 20%, while decreasing the CO2 footprint per produced ton of hydrogen by up to 10%. At the same capacity, the make-up fuel consumption can be reduced by up to 50%.
FUEL SAVING SCENARIO Fuel saving 30 to 50% CO2 footprint of Syngas generation up to 20% reduced Revamp cost for convection section and combustion system limited
CAPACITY INCREASE SCENARIO At increased fired duty up to 20% Fuel consumption up to -30% (decrease) CO2 footprint of Syngas generation up to 10% reduced
Award winning EARTH Technology
EARTH technology has received the ICIS Innovation Award 2022 for Best Process Innovation and the Hydrocarbon Processing Award 2022 for Best Refining Technology.
The recuperative reforming technology combines high-performance with cost-effective CO2 reduction for large-scale hydrogen production. > Learn more
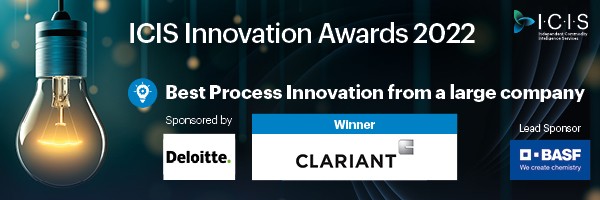
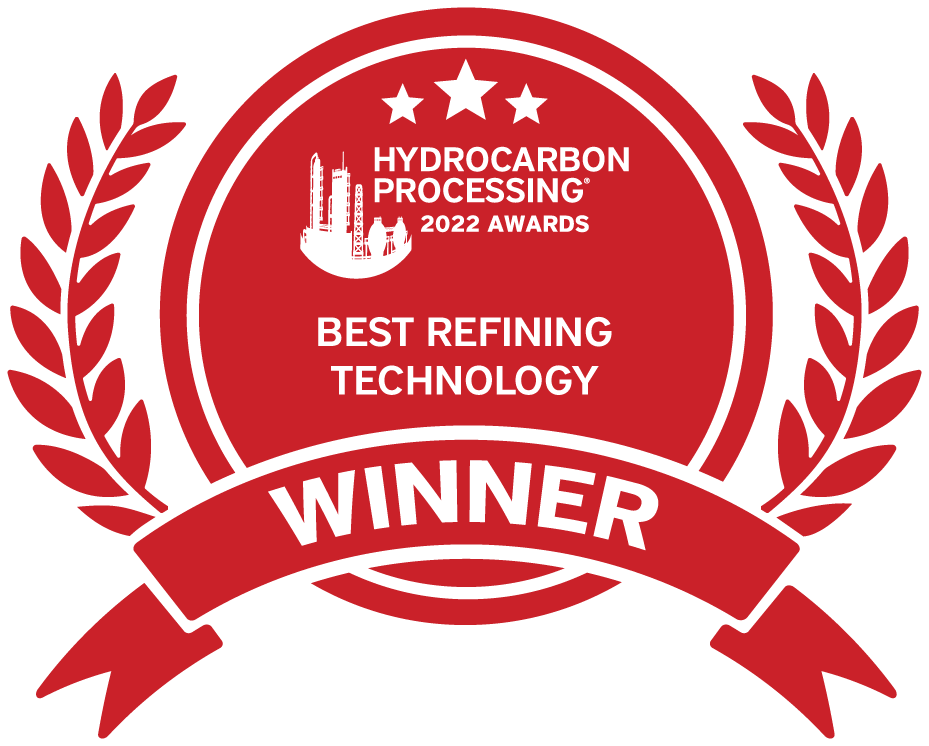
Want to learn more about EARTH Technology?
Blue hydrogen via autothermal reforming
Autothermal reforming is an alternative way to produce syngas composed of hydrogen and carbon monoxide. It involves partial oxidation of the hydrocarbon feed with oxygen together with catalytic steam methane reforming so that almost no external heat is needed. The ATR hydrogen process allows the efficient use of renewable energy to produce oxygen by air separation and to preheat the feed stream, such that, in the best case, CO2 only needs to be captured from the process gas, thus improving sustainability and cost-efficiency of hydrogen production via the ATR route. Clariant’s ReforMax™ ATR series catalysts are especially designed for the demanding ATR process conditions, and offer the high performance needed for stable and long lasting operation.
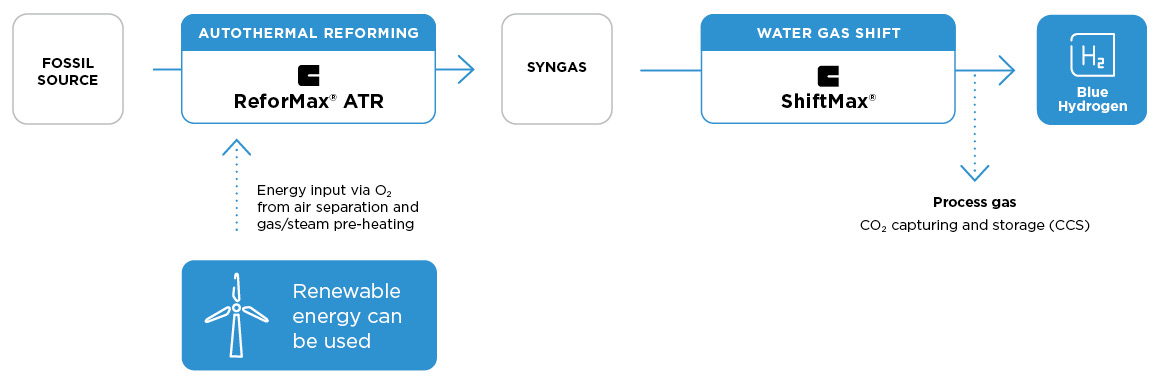
ReforMax ATR series catalysts
Clariant offers technical expertise and optimal solutions for the demanding ATR conditions. Our highly robust ReforMax 330 ATR and ReforMax 331 ATR catalysts are designed to perform optimally, despite reactor exit temperatures in the range of 950-1100ºC.
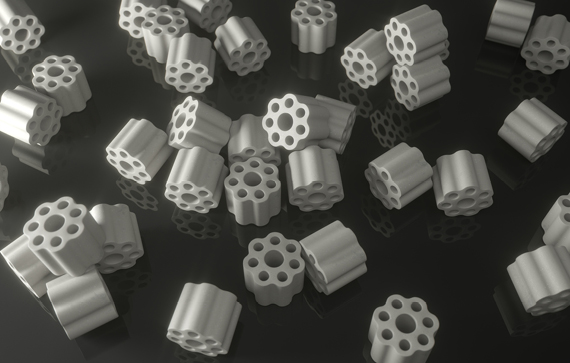
ReforMax 330 ATR series catalysts are commercially proven to be highly active and selective for any process feed and design. The new ReforMax 331 ATR series has a floral 8-hole shape which further lowers pressure drop, enabling even higher gas throughput, and energy savings.
In autothermal reforming, ReforMax 420 ATR is used as an active heat shield to decrease the temperature in the top part of the catalyst bed and to prevent evaporation of nickel and alumina. This avoids their downstream condensation (ruby formation) in the reactor.

Clariant also provides guard layers, tailored to specific reactor designs.
Advantages
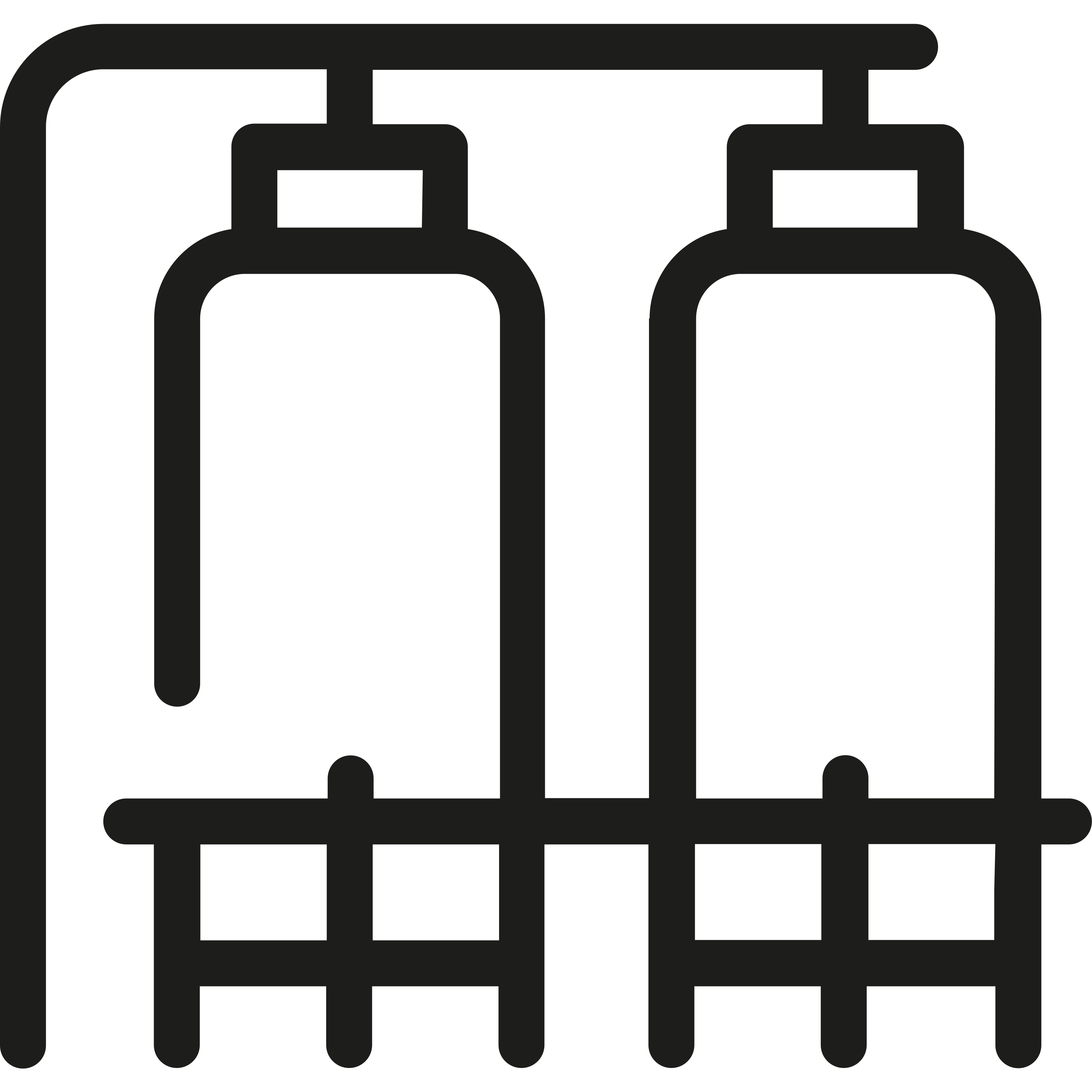
COMPACT DESIGN
small footprint
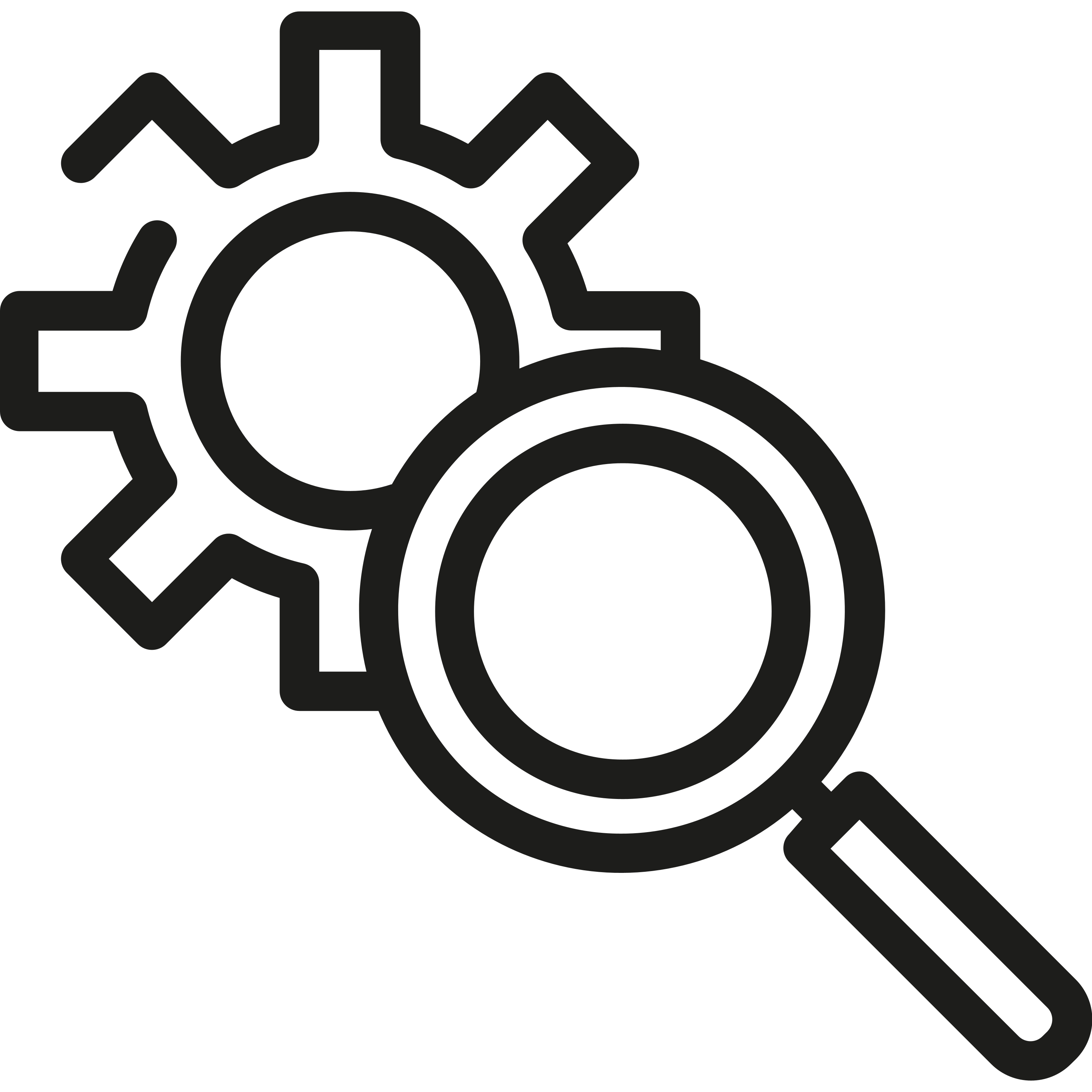
FLEXIBLE OPERATION
Short startup and
fast change outs
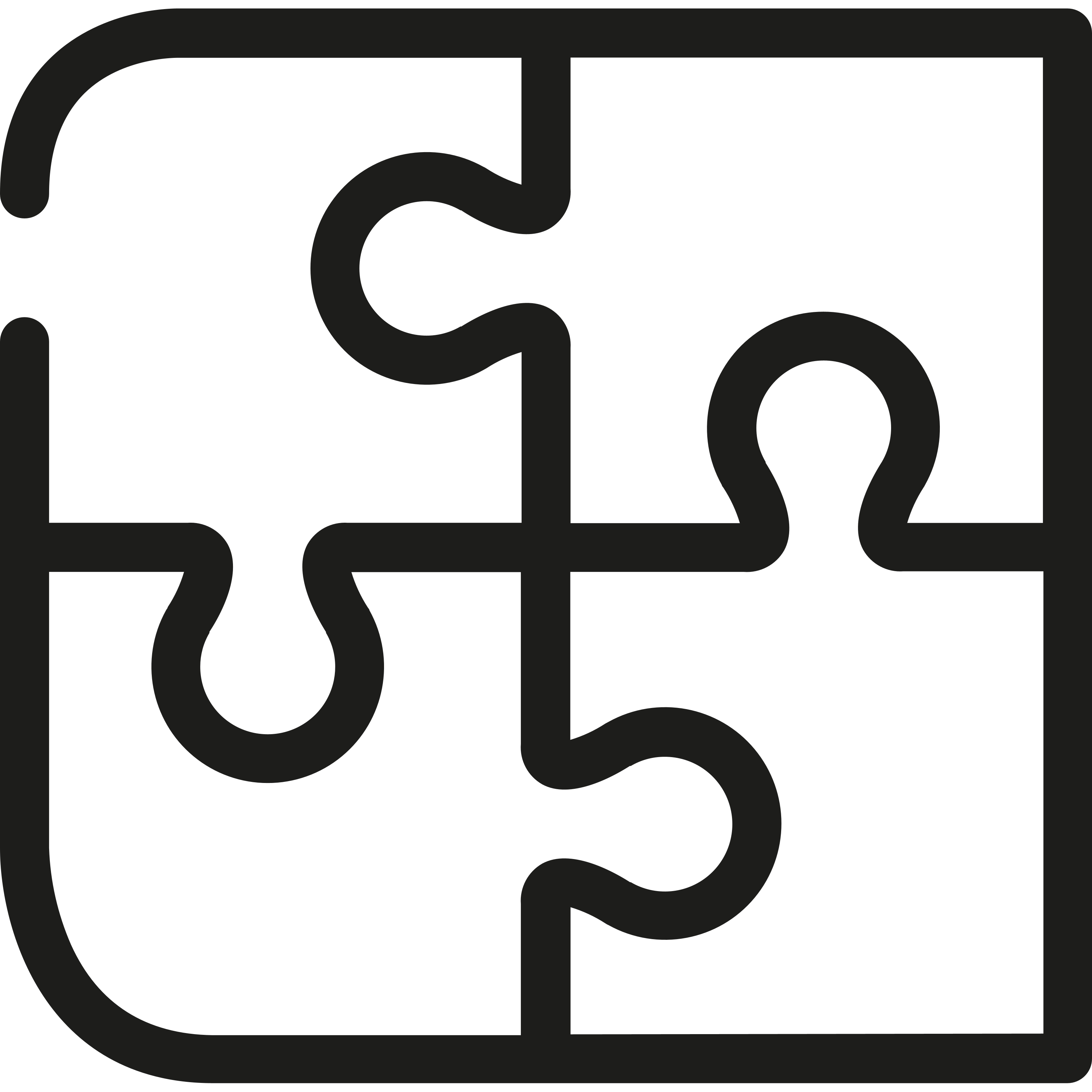
H2:CO FLEXILIBTY
Suitable for many chemicals
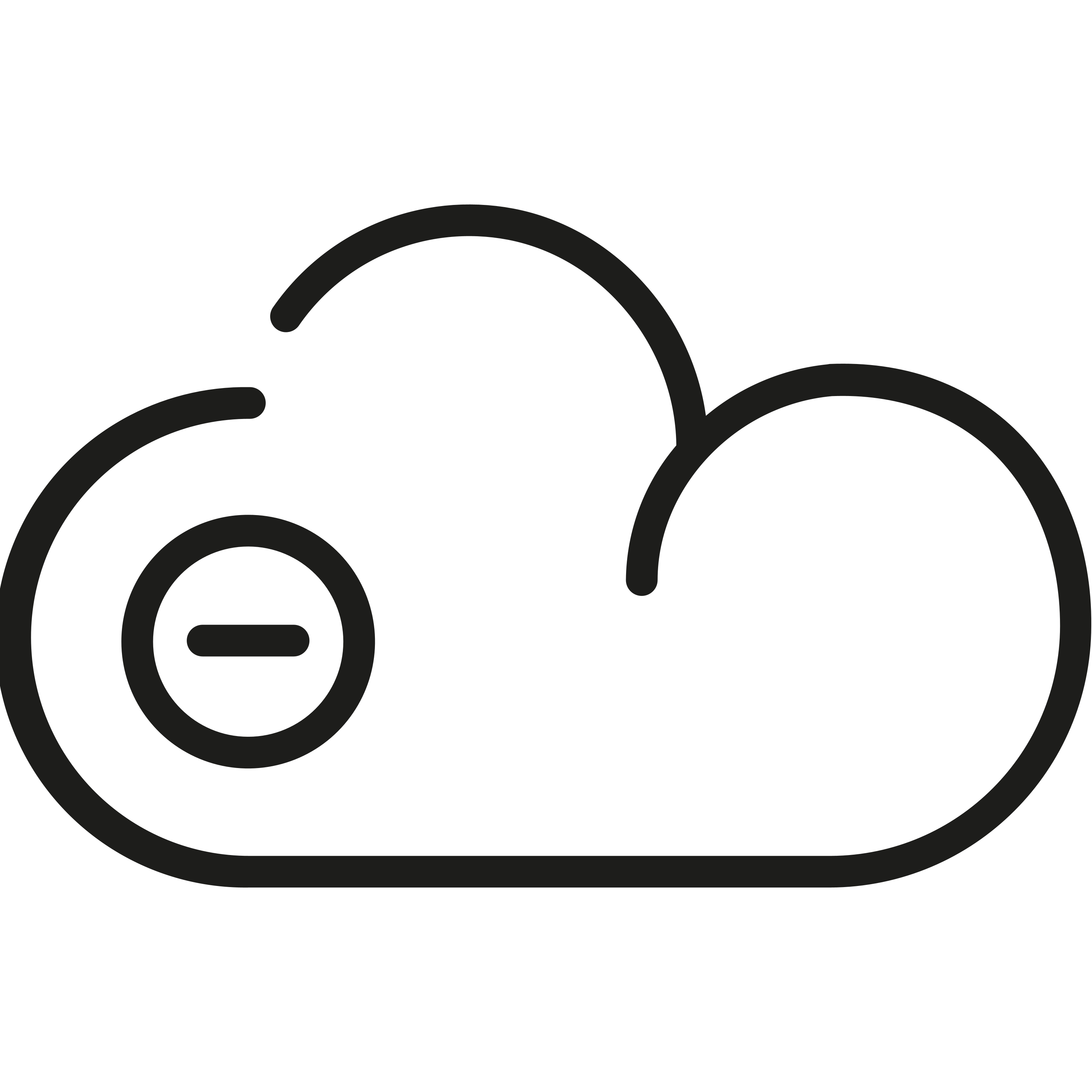
REDUCTION OF
CO2 EMISSIONS
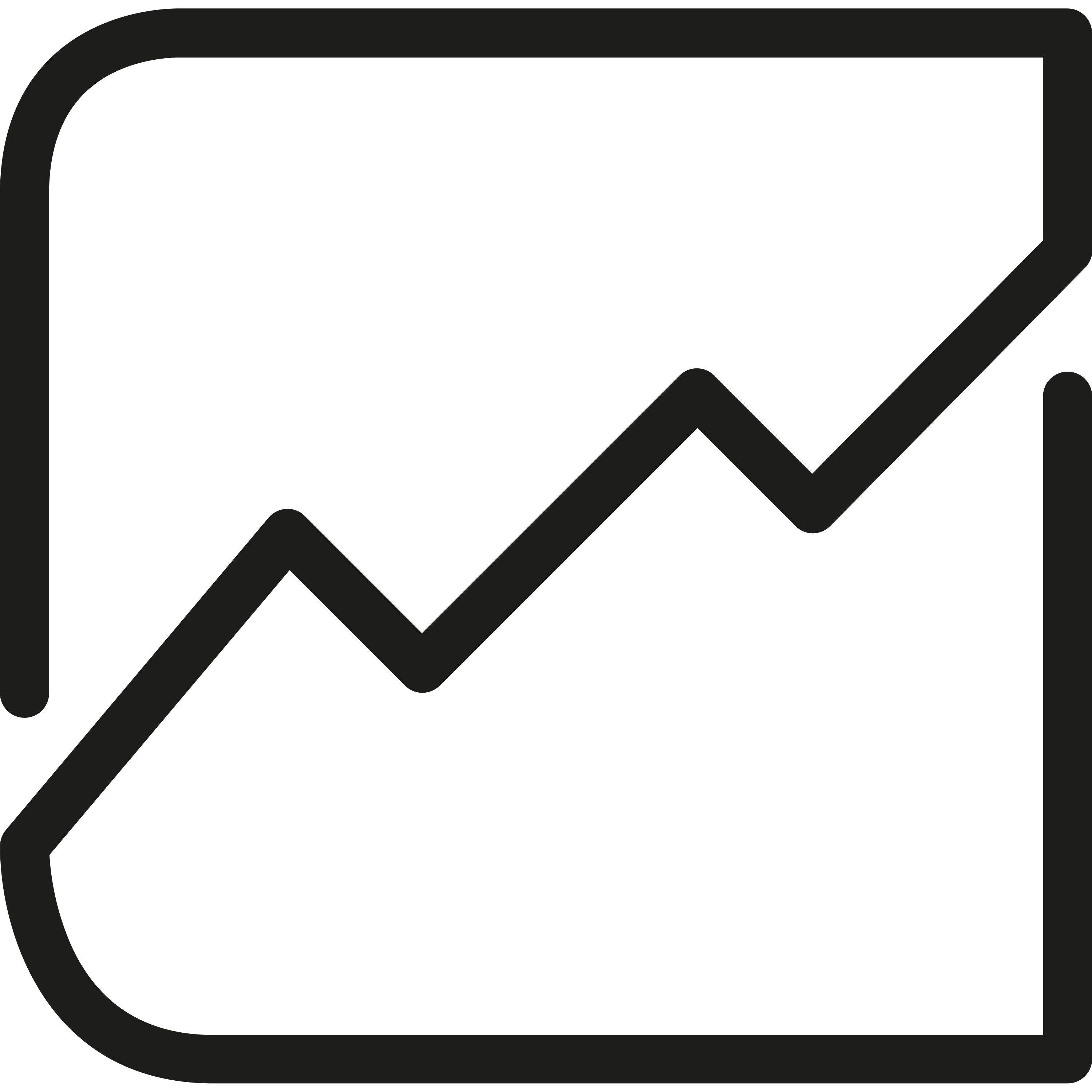
PROFITABLE
At large hydrogen production capacities
Want to learn more about our ATR catalysts?
Blue hydrogen via partial oxidation
In Partial Oxidation process, a mixture of hydrocarbon feedstock and a sub-stoichiometric amount of pure oxygen are reacted to produce a syngas stream with a high CO content of 30-50%, which is converted with steam to hydrogen and CO2 in downstream water gas shift (WGS) reactors. When biomass or municipal waste are used as feedstock and the formed CO2 is captured and sequestrated, the process can be even performed with a negative CO2 footprint. The POX hydrogen process does not require catalysts until the WGS stage, at which point Clariant’s ShiftMax™ 120 high temperature shift catalyst offers the optimal stability and activity required for the challenging process conditions.
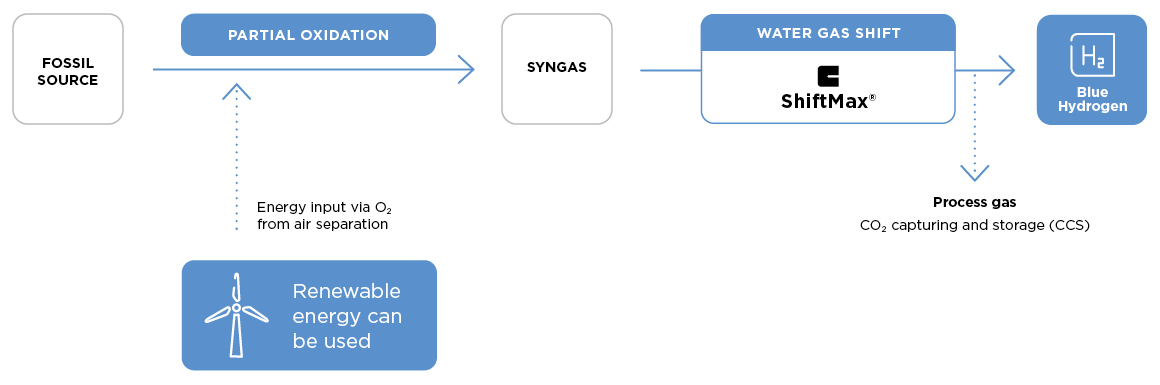
ShiftMax 120 catalyst
The high temperature shift (HTS) catalyst ShiftMax 120 combines high activity and excellent thermal stability with extreme robustness. Thus, it can withstand the CO-rich syngas (30-50% CO) exiting the POX stage, as well as the high temperatures (up to 500ºC) in the adiabatic bed during the shift reaction.
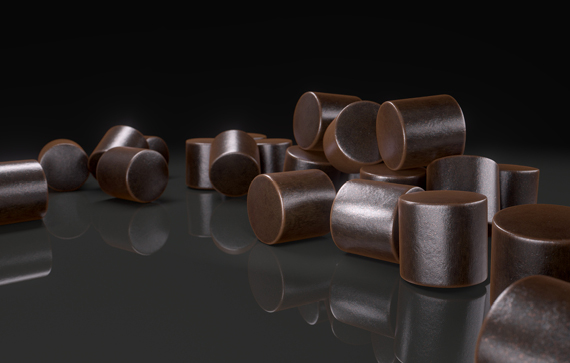
Advantages
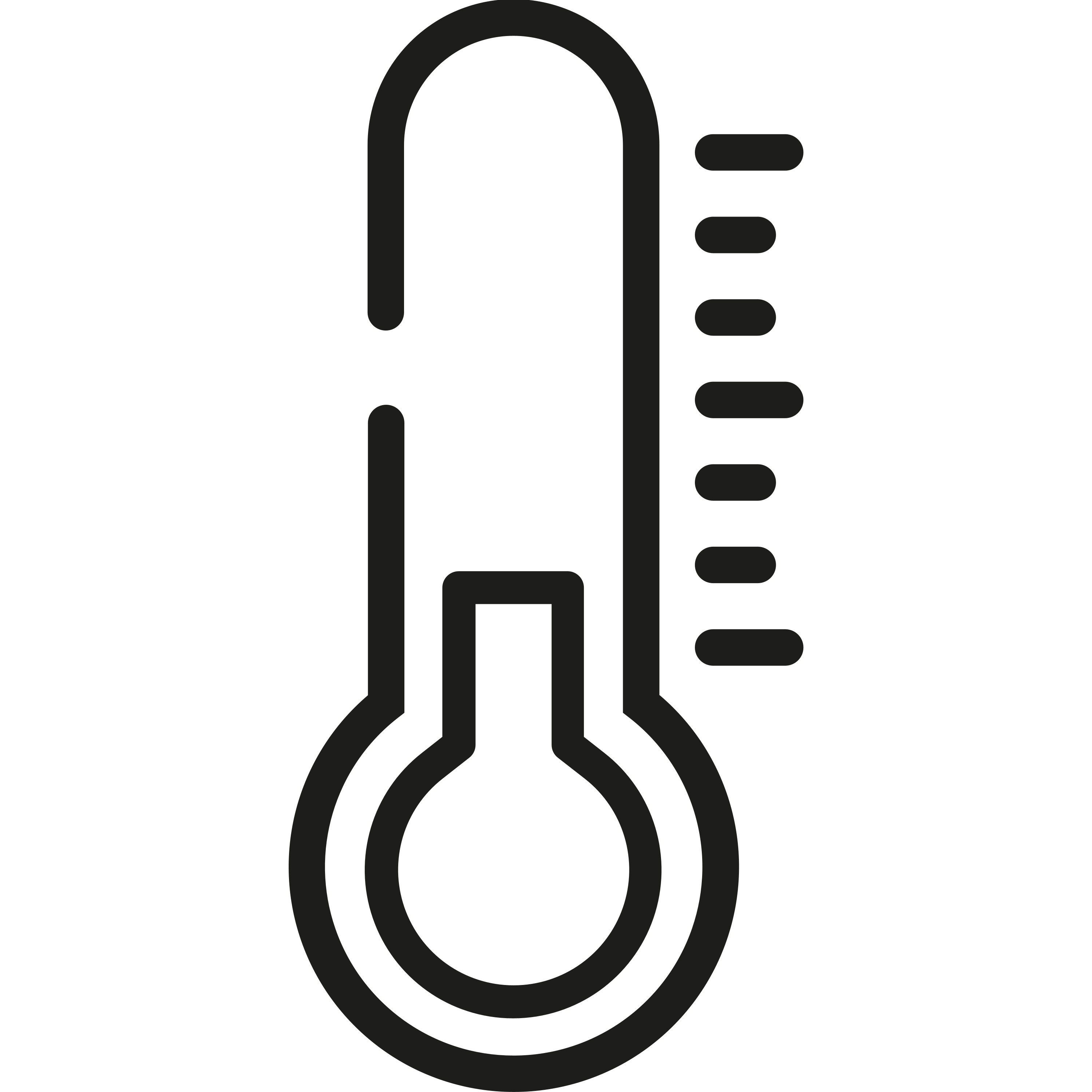
EXTREME THERMOSTABILITY
commercially proven at 500°C
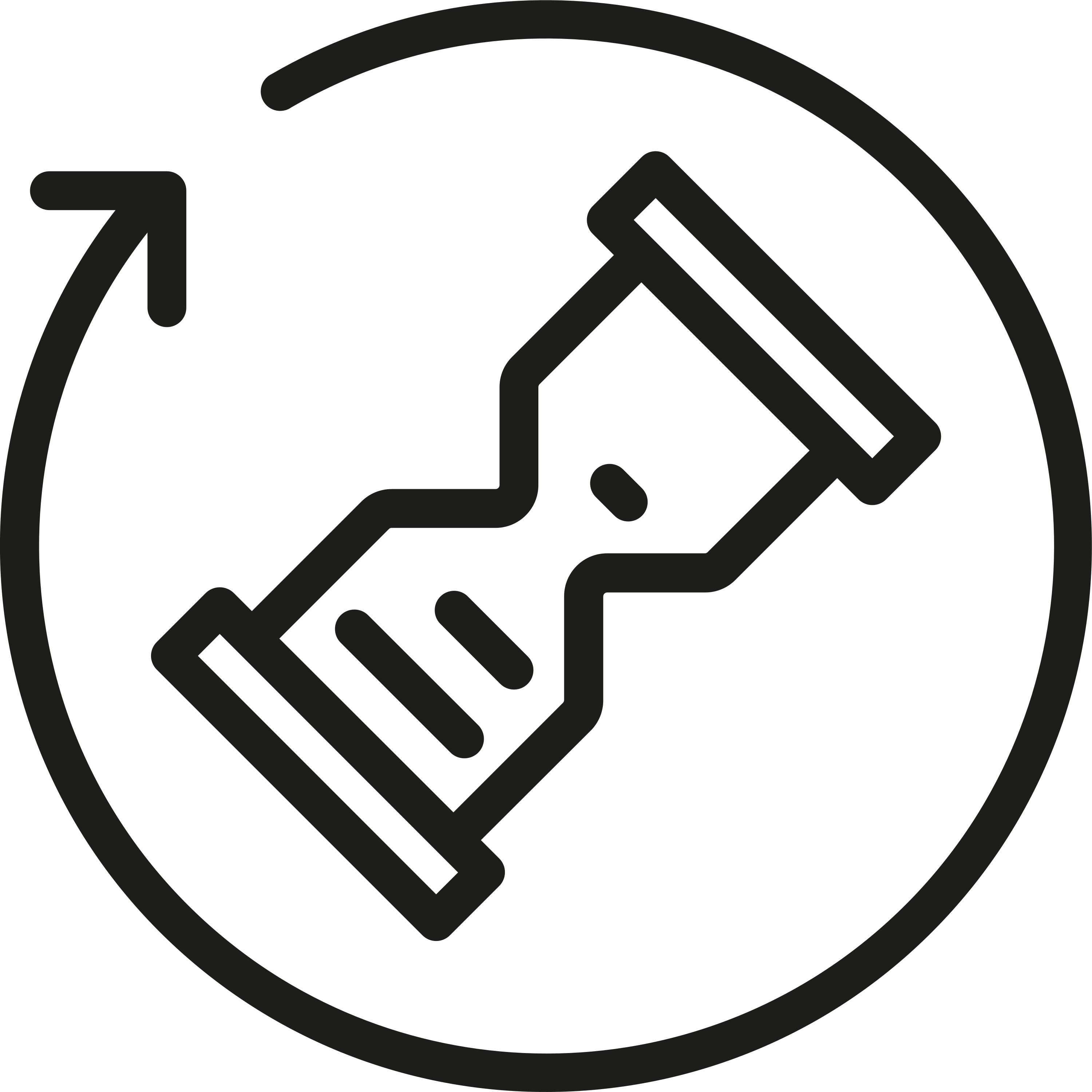
LONG LIFETIME
even at highest CO concentrations
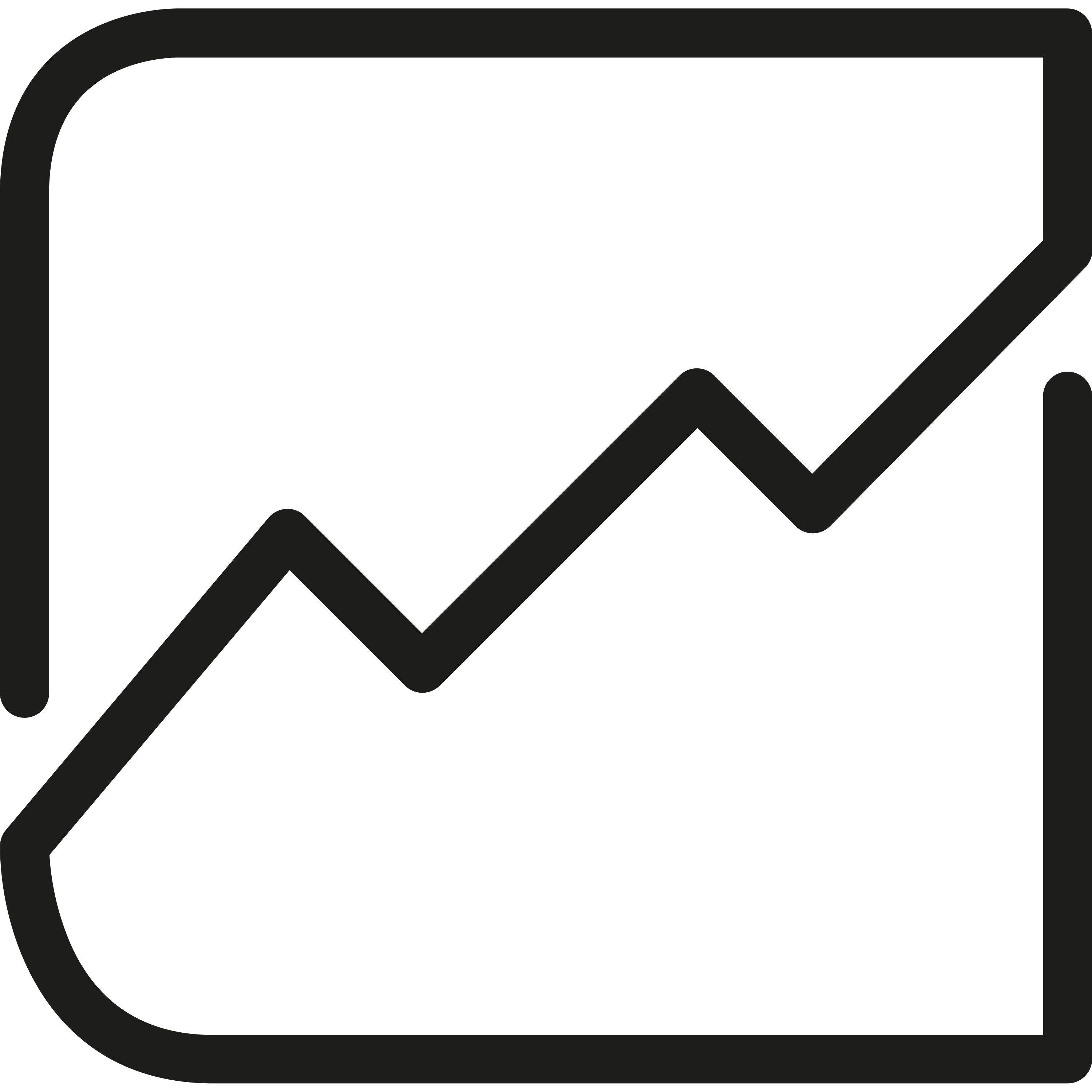
HIGH ACTIVITY
allows conversion close to equilibrium,
even at lower section of catalyst bed with high CO2 concentrations